Once they are up and running, machines and plants require continuous care to maintain optimal performance. Many PID controllers, however, fall victim to a "set it and forget it" approach. The task of constantly checking and adjusting them is simply too time consuming. The situation is much different if you have ready-made software components that allow you to monitor the performance of control loops and make targeted adjustments when necessary.
To provide the necessary redundancy, many plants have multiple similar lines operating side-by-side. Though they may be producing the same products, these lines are generally composed of machines and components from different suppliers. The foremost concern of the plant operator, however, is output alone. When similar lines start showing significant differences in productivity, the search is on to find out why. "What is too often overlooked in this search," says Martin Reichinger, B&R's business manager for process automation, "are the individual machines that make up the lines."
This has a lot to do with the fact that the ability to analyze data at the level of individual machines is a relatively recent development. Today's technologies, however, provide entirely new levels of insight into the machines' inner workings. "With an edge controller," says Reichinger, "you now have easy access to every control loop and every asset – whether it's a heat exchanger or a centrifugal pump – and you can be constantly optimizing their performance."
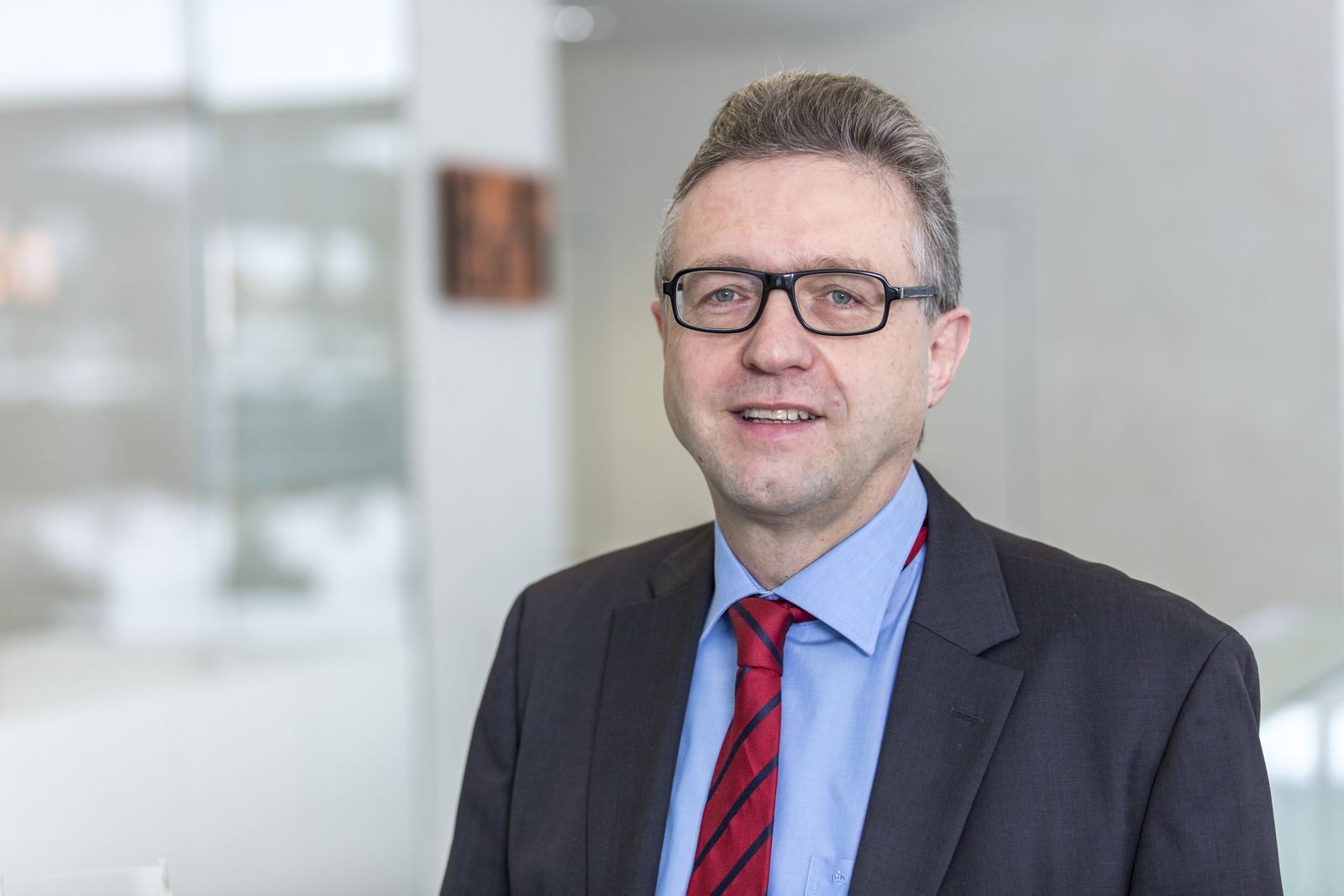
Martin Reichinger, Business Manager – Process Automation, B&R
It's all relative
When setting PID parameters to regulate things like pressure or temperature, engineers have traditionally relied on educated guesses and rules of thumb. "As a result, you have two-thirds of all control loops that, although stable, are not tuned optimally," says Reichinger. That leaves substantial room for improvement. "But, if all you have to work with are the values of a single PID controller, you'll have a hard time deducing which ones are causing trouble," notes the automation specialist. If you're able to compare two similar machines or systems, however, it's much easier – even without any knowledge about the specific process involved.
Evaluation methods based on this type of comparison are known as control performance monitoring (CPM). A CPM module is included in B&R's advanced process control (APC) solution. APROL APC can be used as a standalone solution or as an integrated component of the B&R APROL automation platform. The CPM control module can also be connected to external systems via OPC UA, making it possible to compare data from different sites.

Metrics for evaluating PID loops
B&R's CPM solution makes it possible to evaluate PID loops based on a variety of metrics, and to optimize their settings using efficient tuning methods. One such method is asset monitoring, which is able to identify fouling of heat exchangers or cavitation in centrifugal pumps.
Reichinger's team has developed a number of helpful reporting tools for its CPM solution, including a loop report, which focuses on a single PID loop, and a plant report, which provides overview of multiple loops or an entire plant. "Looking at these reports, you can see which parameters stand out," says Reichinger. "They provide a clear statement about the quality of your PID settings." The CPM solution also shows how many times the operator had to intervene, and how often the control loop reached its limit values.
Optimized with minimal intervention
Once the potential for optimization has been identified using CPM, B&R's APC library offers a number of tuning blocks that apply different methods to automatically determine how the control loop works and calculate the optimal PID parameters. "Traditionally, the user has had to play around with different I or D values and see what happens," explains Reichinger, "but with our blocks, that's no longer necessary."
One of the blocks allows tuning based on the finite-frequency method. "The advantage of this method is that you're able to optimize the controller using very small excitation signals," notes Reichinger. Even an amplitude of ±0.5% for modulation is enough to get a well-tuned PID controller.
Different production processes require different types of control loop. There are split-range loops, alternating loops and many more. "Developing these controllers from scratch is a lot of work," says Reichinger. B&R has simplified the process by developing a variety of control functions that work as add-ons to a classic PID controller. The gain scheduling function, for example, can be used to implement a controller that automatically adjusts the PID parameters based on the operating point. These control functions are listed in the APC library along with the tuning blocks.
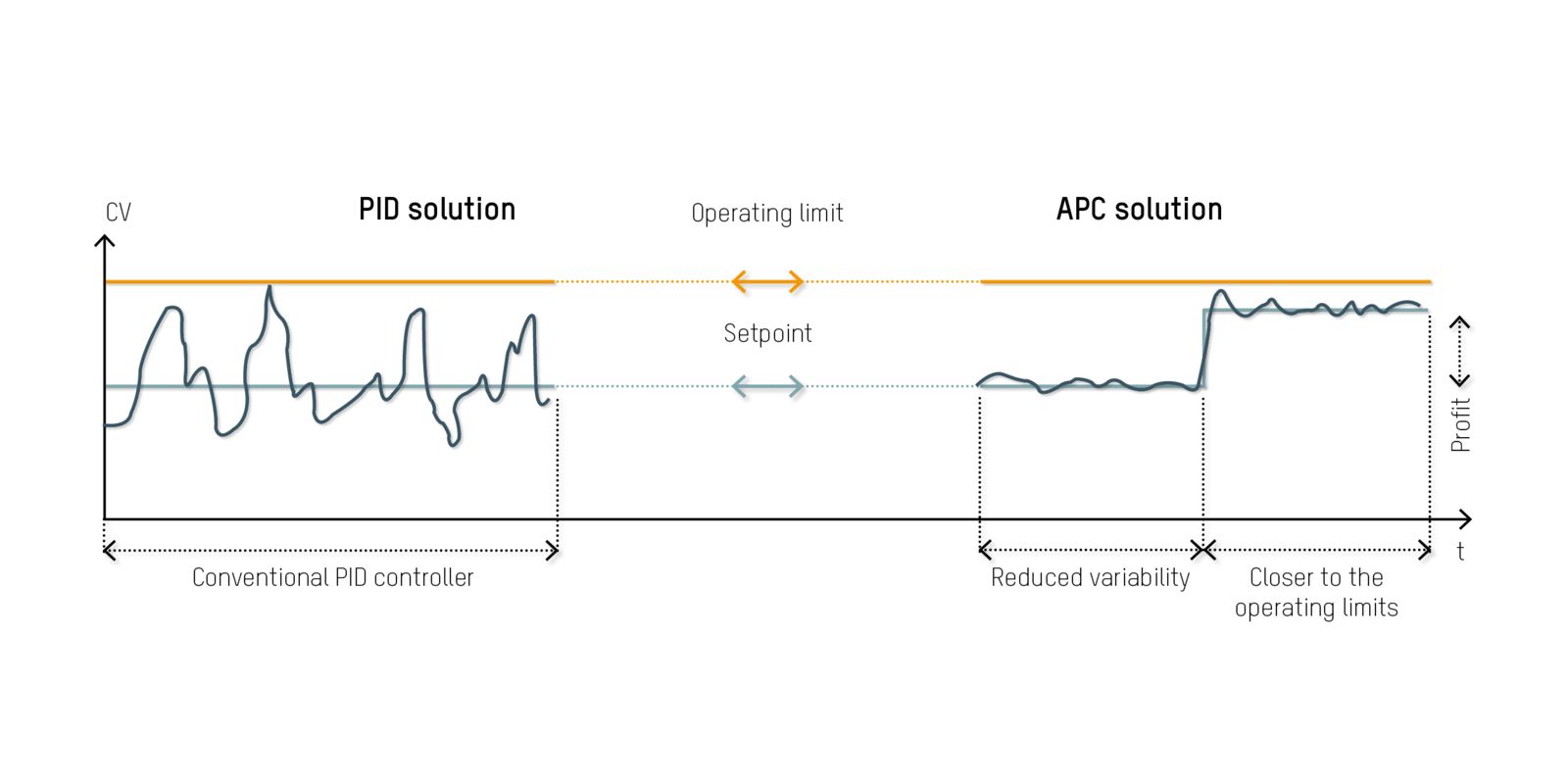
Defining operating limits
When a control loop has multiple variables that interact with each other, a classic PID controller is not sufficient. "That doesn't keep most developers from trying to use them, though," says Reichinger. Not only does this result in suboptimal control performance, it can bring down the whole machine or plant if a value gets out of control.
"You can get substantially better results in these cases with a multi-variable controller," argues Reichinger. That's why B&R developed a model predictive controller (MPC) that supports multiple controlled, disturbance and manipulated variables – up to ten each. While the MPC does have to be set empirically, according to Reichinger, the job is manageable: "Using the faceplate, automation engineers simply select the desired transmission behavior and set a few parameters. With a few rounds of optimization, they should be able to have an MPC running optimally." The introduction of the MPC controller has yielded some impressive results thus far. "Plants that had been experiencing multiple unplanned stoppages per week suddenly run smoothly for months on end after switching to MPC," recalls Reichinger.

Unlike the PID controller, MPC allows the user to define limits that are not permitted to be crossed. But how is that possible? "MPC uses a model of the process to continuously calculate how the values will progress in the future," explains Reichinger. This enables the controller to determine early on when a value is in danger of violating its limits and make the necessary corrections before a violation occurs. "Stoppages can be almost entirely eliminated." Effectively ensuring that the limits are not exceeded also makes it possible to run the process closer to its operating limits.
Greater efficiency through optimized control loops
Modern technology makes it easy to continuously monitor and adapt the performance of control loops and manufacturing assets. This enables operators to maintain optimal control settings and run their processes closer to their limits. "An optimized control loop helps prevent unplanned downtime, making machines and plants more efficient and profitable to operate," says Reichinger.
Author: Carmen Klingler-Deiseroth, freelance journalist
Flexible solution package
The sophisticated control algorithms of APROL APC aren't just available to those using the APROL process control system. They can also be implemented in existing plants as a standalone solution preinstalled on an industrial PC that requires no expert knowledge to use. The same industrial PC can double as an edge controller, aggregating data and sending it to higher-level systems – even into the cloud – for analytics and other services.