Producenci na całym świecie dążą do zbudowania nowej generacji inteligentnych fabryk. Indyjscy producenci nie są tu wyjątkiem – kończąc etap oceny, przystępują do wdrażania zaawansowanych technologii, które pozwolą im stawić czoła przyszłym wyzwaniom. Rolę lidera wśród tych producentów przejęła firma Plastech Solutions, która połączyła wypracowane dotąd rozwiązania w całkowicie zintegrowany system. Do osiągnięcia takiego poziomu integracji potrzebne było bogate, modułowe i skalowalne rozwiązanie problemu automatyzacji. Konstruktorzy z Plastech Solutions zaufali systemowi APROL firmy B&R jako idealnie spełniającemu wszystkie wymagania.
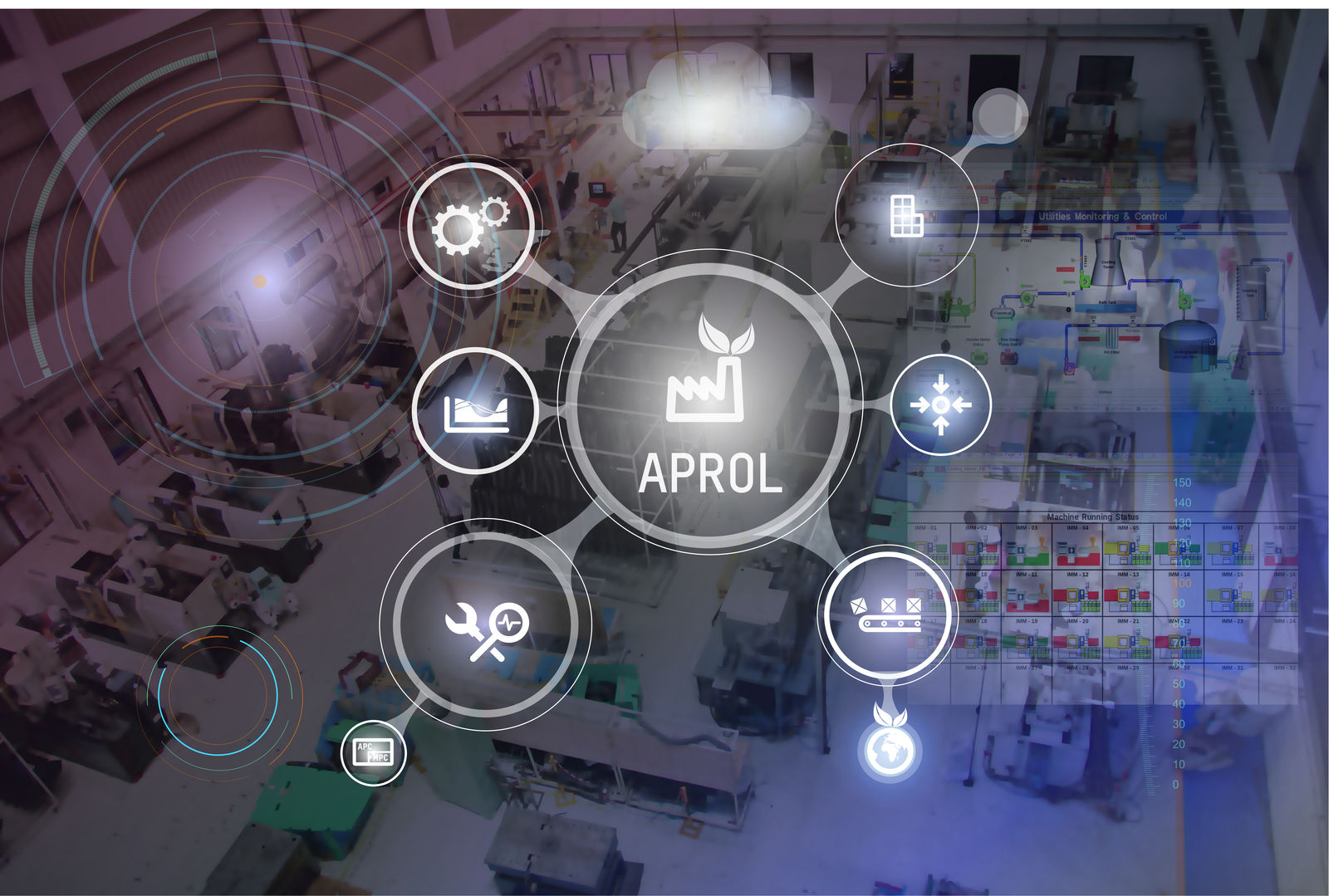
Firma Plastech Solutions ma cztery zakłady produkcyjne w różnych lokalizacjach w Pune w Indiach, specjalizujące się w produkcji elementów plastikowych dla przemysłu motoryzacyjnego, lotniczego i kosmicznego, do produkcji aparatury rozdzielczej i elementów infrastruktury, a także urządzeń konsumenckich. Firma posiada również dział automatyki, który spełnia wymagania fabryk poszukujących możliwości zastąpienia starszych sterowników najnowszymi rozwiązaniami w zakresie sterowania maszynami i ruchem lub modernizacji maszyn w celu zwiększenia sprawności energetycznej. Jako centrum indyjskiego przemysłu motoryzacyjnego, Pune stanowi doskonałą platformę dla rozwiązań Plastech. Firma jest dostawcą pośrednim znanych indyjskich i międzynarodowych producentów samochodów.
Eliminowanie strat w celu poprawy sytuacji
Wszyscy producenci dążą do zwiększenia rentowności, a zmniejszenie strat odgrywa w tych dążeniach kluczową rolę. Źródłem problemów fabryki, mającym istotny wpływ na jej rentowność, mogą być różne, niedostrzegane na co dzień straty. „Nasza fabryka działa od ponad 12 lat i jej produktywność nie budziła naszych zastrzeżeń” – mówi założyciel i dyrektor generalny Plastech, Ajay Zod. „Mimo to, nieustając w konsekwentnym dążeniu do doskonalenia procesów produkcyjnych, postanowiliśmy wdrożyć rozbudowane rozwiązanie służące do monitorowania strat.”
Rozwiązanie miało na celu ograniczenie strat ponoszonych w toku produkcji i gospodarowania zapasami, a także ograniczenie zużycia surowców i energii. W firmie dostrzeżono, że sprawność fabryki mierzona stosunkiem produkcji rzeczywistej do planowanej wynosi tylko 60%, a przyczyną jest marnotrawstwo, którego nikt nie analizuje. W wielu przypadkach silniki działały nawet wtedy, gdy dana maszyna pozostawała bezczynna. Takie sytuacje prowadzą do marnowania energii i mają duży wpływ na rentowność.
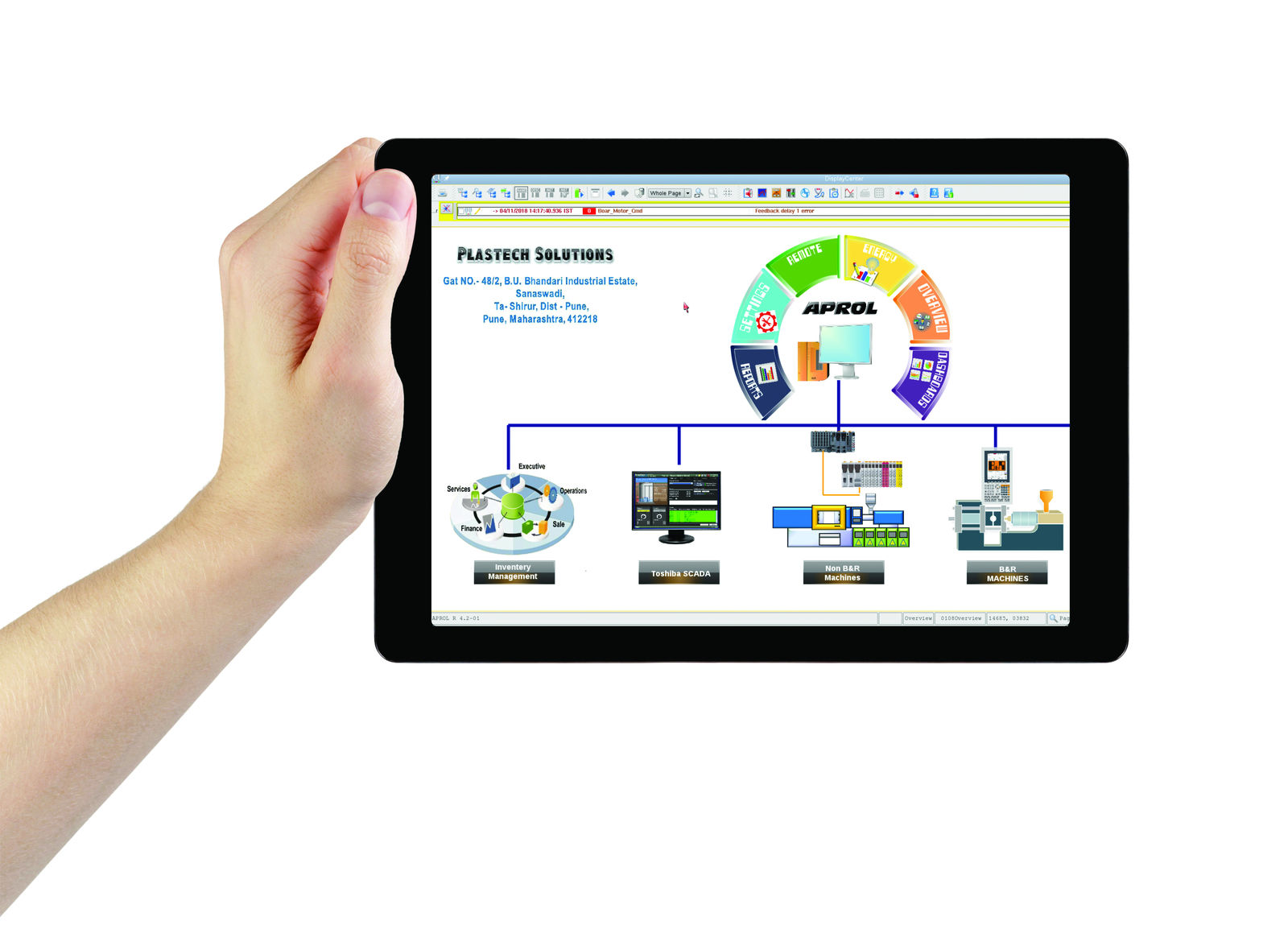
Zintegrowany zakład produkcyjny
Od tego czasu firma Plastech przekształciła swój zakład produkcyjny w prawdziwie inteligentną fabrykę. Zakład posiada obecnie 40 wtryskarek umożliwiających wytwarzanie produktów i komponentów z 40 różnych form. Firma Plastech nie tylko zintegrowała komunikację pomiędzy systemami hal produkcyjnych i systemami informatycznymi – w jednym systemie zintegrowano także narzędzia, zarządzanie zapasami, zarządzanie finansami, automatyzację infrastruktury, pomiar ogólnej efektywności urządzeń (OEE), operacje i sprzedaż.
Planowane jest również połączenie i integracja czterech zakładów produkcyjnych w innych lokalizacjach. System automatyki zakładowej monitoruje każdą maszynę na hali produkcyjnej i łączy ją z systemem centralnym. Zebrane dane są wykorzystywane do obliczenia ogólnej efektywności urządzeń (OEE) dla każdej maszyny. Produkty schodzące z maszyny są identyfikowane jako dobre lub złe i odrzucane jako odpad lub odpowiednio selekcjonowane do wysyłki. Kruszarka na hali produkcyjnej przekształca odrzucone produkty w granulki, które są ponownie wykorzystywane do produkcji nowych produktów. Ten etap pozwala zaoszczędzić sporo surowca.
Fabryczne systemy oddymiania i przeciwpożarowe są również zintegrowane z tym samym centralnym systemem automatyki. Umożliwiają wczesne wykrywanie ognia, a w efekcie zmniejszenie zużycia wody. Stan wody chłodzącej potrzebnej w różnych maszynach jest również monitorowany przez system automatyki zakładowej. System utrzymuje poziom wody, a także dostarcza dodatku chemicznego do chłodzenia. W wieży chłodniczej monitorowana jest zarówno temperatura, jak i ciśnienie. Główna brama fabryki jest monitorowana przez kamerę IP, a nagranie jest rejestrowane w systemie automatyki zakładowej.
Do wizualnej prezentacji monitorowanych maszyn i urządzeń służą różne wykresy trendów. „Połączyliśmy i zintegrowaliśmy wszystkie możliwe komponenty w naszej fabryce – wszystkie są monitorowane 24 godziny na dobę, 7 dni w tygodniu. Pomogło nam to osiągnąć wyższą produktywność i ogólną efektywność urządzeń, a jednocześnie zmniejszyć marnotrawstwo, koszty zapasów i straty” – mówi Zod.
APROL poprawia ogólną efektywność urządzeń
„Kiedy rozpoczęliśmy dyskusję na temat projektu, celem było jedynie monitorowanie zużycia energii w naszych systemach” – wspomina Zod. „Jednak w trakcie dyskusji z ekspertami B&R szybko zdaliśmy sobie sprawę z wielu korzyści biznesowych, które można osiągnąć dzięki posiadaniu jednego systemu kontroli procesów, pozyskiwania danych, monitorowania, analizy i długoterminowego przechowywania danych.” Potężne rozwiązanie APROL firmy B&R na potrzeby automatyzacji zakładów służy teraz jako pojedynczy system sterowania i monitorowania fabryki Plastech.
Kierownik produkcji korzysta codziennie z pulpitu nawigacyjnego APROL, aby przydzielać operatorów do poszczególnych maszyn na hali produkcyjnej i dobierać formy do produkcji. Jest to pomocne w równoczesnym monitorowaniu wydajności maszyn i operatorów. Wszelkie odchylenia generują sygnały ostrzegawcze i są rejestrowane na potrzeby analizy. APROL umożliwia sporządzanie kompleksowych raportów, prezentację trendów i rejestrację danych historycznych. Dostęp do tych raportów można uzyskać również za pomocą smartfona lub tabletu. Dane dotyczące dostępności, produktywności i jakości są przekształcane przez APROL w cenne informacje, takie jak wskaźniki ogólnej efektywności urządzeń dla zarządzających fabryką.

Cud architektury
W hali produkcyjnej zainstalowane są maszyny wielu producentów, co znacznie utrudnia gromadzenie danych. System APROL łączy się z rozwiązaniami B&R, maszynami różnych producentów i systemami SCADA za pomocą sieci Ethernet i protokołu OPC UA. Sterowniki bez natywnej opcji łączności są podłączane za pomocą dodatkowych modułów I/O X20 i okablowania równoległego. Narzędzia są kontrolowane i monitorowane za pomocą modułów I/O X20 połączonych w architekturze zdecentralizowanej.
Na Automation PC 910 pracuje system operacyjny Linux, serwer inżynieryjny APROL i serwer wykonawczy. Jest on połączony ze stacją operatorską umieszczoną centralnie w dyspozytorni z widokiem na halę produkcyjną. Architektura zdecentralizowana ułatwia podłączanie poszczególnych maszyn i urządzeń do centralnego Automation PC 910. Moduły X20 I/O są podłączone poprzez, deterministyczną, niezależną od dostawcy sieć open-source POWERLINK. Pozwala to zmniejszyć nakłady na okablowanie i konserwację w fabryce oraz poprawia diagnostykę. Automation PC 910 zapewnia również długoterminowe przechowywanie danych historycznych i raportów.
Plastech ma możliwość dalszego zwiększania przestrzeni pamięci dzięki korzystaniu z usług w chmurze. APROL może łatwo łączyć się z różnymi platformami chmury przy użyciu otwartych protokołów, takich jak OPC UA, MQTT i AMQP. Modułowy system I/O X20 ułatwia firmie wybór konkretnej funkcjonalności I/O wymaganej dla danego narzędzia, czy maszyny. Pozwala to zmniejszyć koszty i zwiększyć elastyczność procesu i systemu pozyskiwania danych.
„Możliwości sprzętu i oprogramowania B&R zrobiły na nas duże wrażenie” – potwierdza Zod. Dzięki obsłudze rozwiązań open-source, takich jak Linux, POWERLINK i OPC UA, firmie Plastech łatwiej jest uniezależnić się od dostawców na poziomie maszyny, fabryki i chmury. „Nieszablonowe rozwiązanie monitorowania zużycia energii i pozyskiwania danych procesowych, wraz z konfigurowalnymi raportami, stanowi o wyjątkowym charakterze systemu APROL oferowanym przez B&R” – zauważa.
Rozwiązanie APROL EnMon jest obecnie wykorzystywane do monitorowania zużycia energii w całym zakładzie. Moduł pomiaru energii X20AP3131 zapewnia kompaktowe połączenie na potrzeby zasilania wejściowego. Obniża to dodatkowe koszty komponentów systemu i umożliwia firmie Plastech łatwą i szybką integrację rozwiązań.
Spojrzenie w przyszłość
„Z powodzeniem wdrożyliśmy system APROL w naszym zakładzie produkcyjnym i korzyści stąd wynikające są już widoczne” – mówi Zod. "Planujemy pomnożyć te korzyści poprzez połączenie wszystkich naszych zakładów.
W przyszłości planujemy dodać monitoring energetyczny poszczególnych maszyn i urządzeń, co pozwoli nam pozyskiwać zindywidualizowane dane. „Myślimy również o integracji zależnej od stanu konserwacji predykcyjnej we wszystkich naszych maszynach poprzez zastosowanie rozwiązania APROL ConMon” – podsumowuje Zod.
![]() | Ajay Zod Dyrektor Generalny Plastech Solutions „Możliwości sprzętu i oprogramowania B&R zrobiły na nas duże wrażenie. Dzięki obsłudze rozwiązań open-source, takich jak Linux, POWERLINK i OPC UA, łatwiej nam uniezależnić się od dostawców na poziomie maszyny, fabryki i chmury. Nieszablonowe rozwiązanie APROL, wraz z konfigurowalnymi raportami, stanowi o wyjątkowym charakterze systemu APROL oferowanym przez B&R.” |