To implement safety solutions economically at different scales, machine builders have generally been forced to develop entirely different concepts for each machine variant. Not anymore, however. B&R's freely-scalable integrated safety is available at prices that can compete with conventional relay technology.
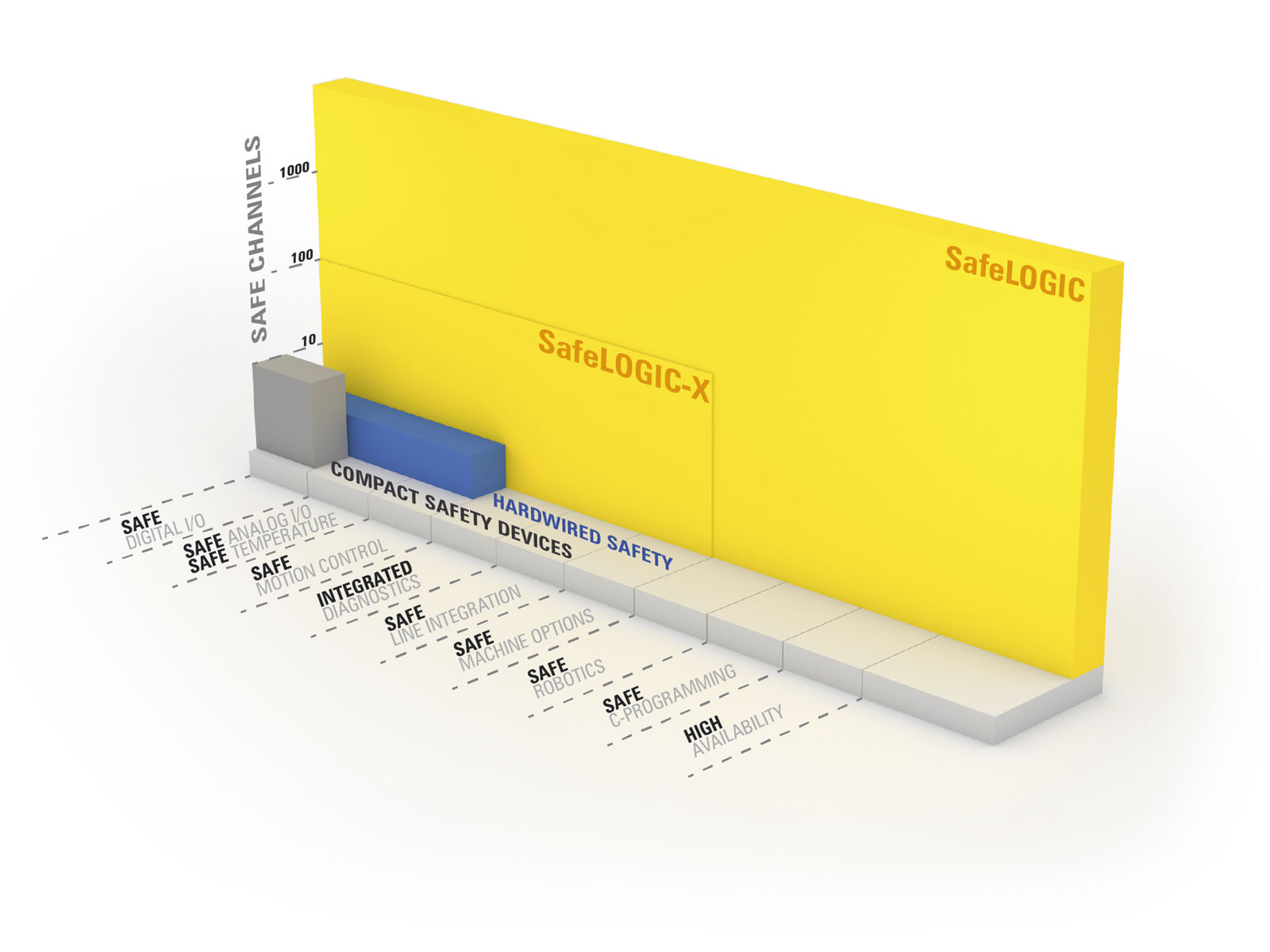
Long gone are the days of the traditional series-built machine with identical units produced cookie-cutter style in large quantities. To compete, today's machine builders must instead offer multiple variants of each machine, typically taking the form of high-end, entry-level and midrange configurations. A given machine is then often further specialized with custom options and adaptations for specific markets.
"What you generally have," explains Franz Kaufleitner, B&R's product manager for integrated safety, "is an original machine design, which then becomes the basis for an array of variants and options." This requires extensive additional work, even for the standard control technology. "It becomes even more problematic when it comes time to design the safety technology for the many different configurations," emphasizes the safety expert.
Affordable hardware
For low-end machines with limited functionality, machine builders still frequently rely on hardwired safety technology. For variants with more demanding requirements, on the other hand, programmable safety technology is standard. That means that a machine builder who wants to adapt a high-end machine for a cost-sensitive market would need to switch from a programmable solution to a hard-wired one.
"That approach sends them all the way back to the drawing board to develop a new safety application," says Kaufleitner. Not only that, but they now have multiple safety concepts to be documented, archived and kept up to date. Clearly, the more efficient and cost-effective solution would be to have a singe safety application that can be used with every machine configuration.
For that to work, however, there are two criteria that must be met. "First, you need to have affordable hardware for implementing integrated safety at the smallest scale," notes Kaufleitner. "Second, you need full system continuity, so that the software runs equally well on whatever hardware is selected." These were the challenges Kaufleitner and his team faced in developing B&R's ultra compact, software-compatible safety controller.
SafeLOGIC-X now makes it possible to implement integrated safety technology at a price that compete with hardwired relay technology or compact safety devices. But how is that possible? "We distributed the tasks normally performed by a safety controller across components already found in the automation system," says Kaufleitner. "That's why we also call the solution a virtual safety controller, because it doesn't rely on a physical safety controller."
SafeLOGIC-X is a safe I/O module with additional processing resources and offers all the functionality of a full-fledged SafeLOGIC controller. The safety application runs on the SafeLOGIC-X module, while safe parameter handling and configuration management – both certified for SIL3 / PLe / Category 4 – run on the standard controller.
Enthusiastic user feedback
Integrated safety technology has a reputation for being complex and expensive. With its easy-to-use software tools and SafeLOGIC-X controllers, however, B&R has proven that it can be anything but. "The first time our customers use the virtual safety controller," reports Kaufleitner, "they're amazed by all the possibilities it opens up for them."
Whereas hardwired safety technology offers a single reaction – cutoff – SafeLOGIC-X also supports B&R's extensive safe motion control functions and ultrafast response times. "It makes small machines both safer and more flexible," emphasizes Kaufleitner. The machine doesn't have to react to a safety event by shutting down, but instead can perform much more nuanced responses that are fine-tuned to the defined safety requirements (see info box). Until now, the cost factor has reserved this type of sophistication for larger applications.
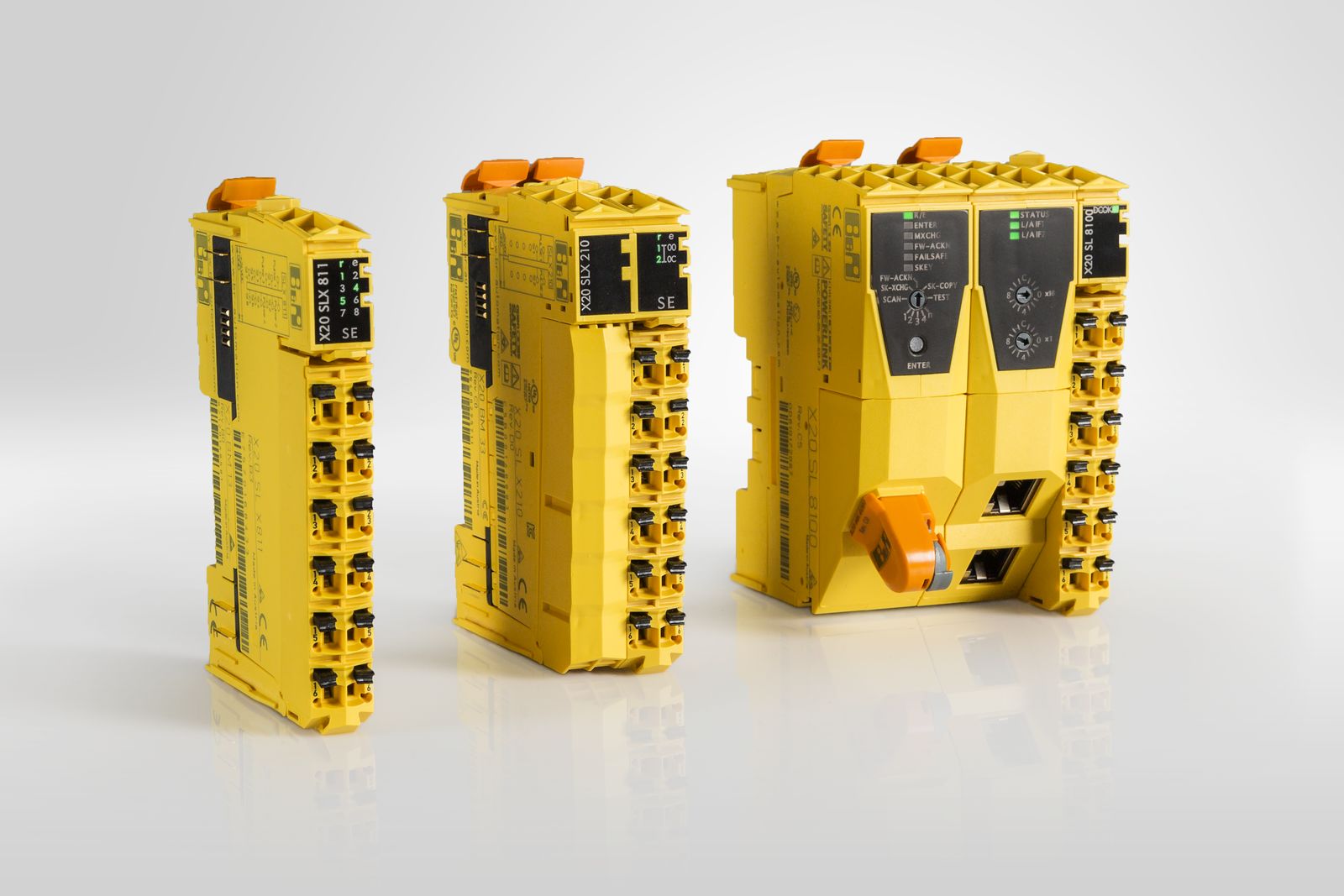
One tool is all you need
With B&R's scalable solution, every machine and variant can be programmed in the same development environment. The programming interfaces, functions and module configuration are all the same, regardless of which safety controller is used. Developers only need to learn one system. SafeLOGIC-X also supports all the advantages of modular machine design and integrated diagnostics.
With all these possibilities, the only limit to what new solutions developers can create is their imagination. It's even possible to combine the virtual and standard safety controllers – as has been done with understage lift systems, for example. "These systems have numerous elements that need to function autonomously," says Kaufleitner, "but on the other hand, they also need to perform precisely coordinated movements."
It can also be that an end customer requests a machine configuration that exceeds the capabilities of an existing SafeLOGIC-X solution. In this case, the machine builder can simply switch to a more powerful SafeLOGIC controller. "All of the existing programming can still be used," says Kaufleitner. B&R's solution makes integrated safety technology consistent and scalable across all machine types and variants.
Safety technology for high availability
Integrated safety technology makes machines more flexible as well as safer. "After all, they're no longer being tampered with," says Kaufleitner. It's a topic many are reluctant to talk about, but when briefly opening a safety door brings production to a halt, operators are tempted to manipulate the door contact. With programmable safety, on the other hand, production can continue even while the door is open – at reduced speed if necessary. It is even possible to allow direct intervention without triggering a cutoff. This not only increases the machine availability, it removes the motivation to manipulate the safety equipment.
Author: Carmen Klingler-Deiseroth, freelance journalist
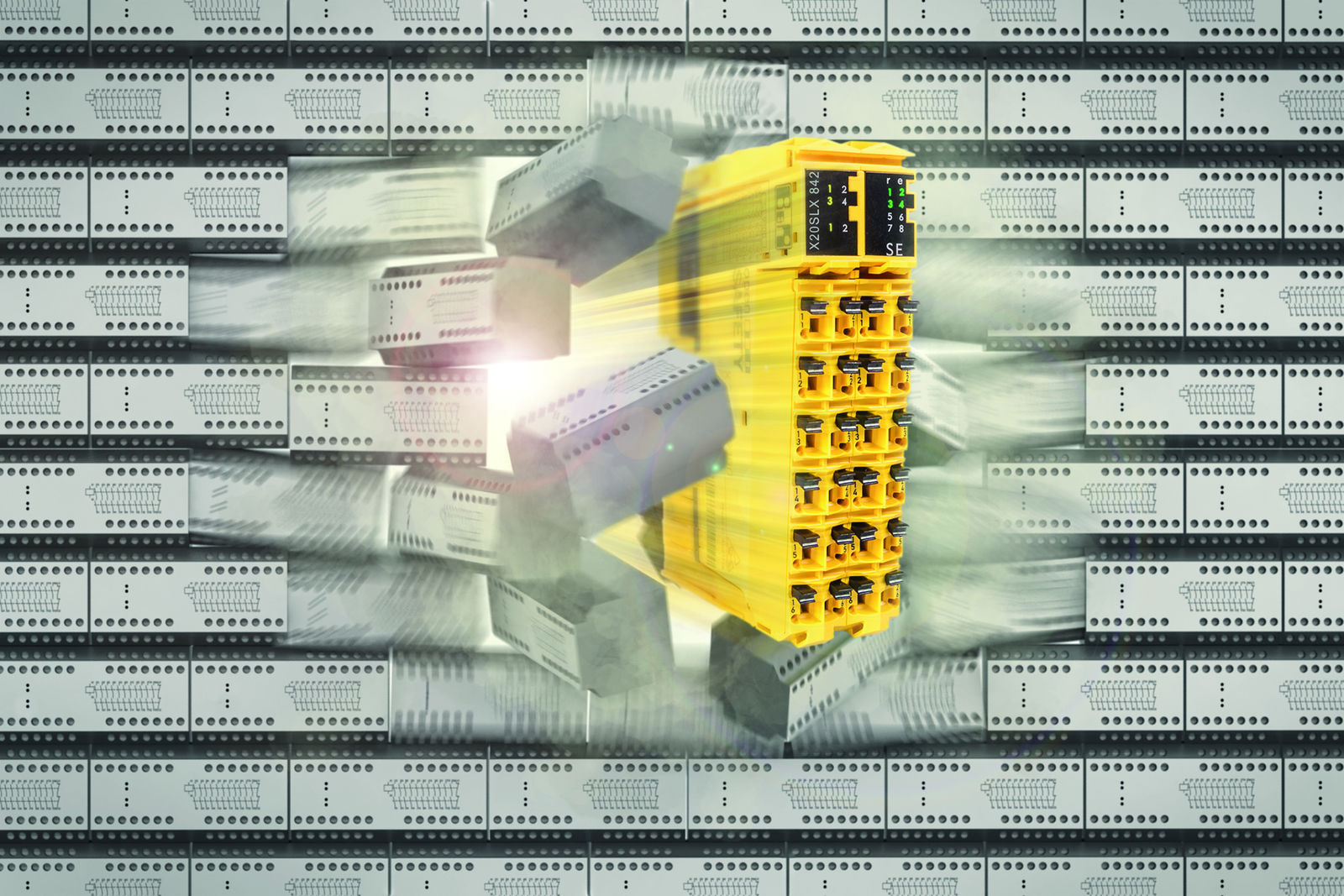