In addition to being efficient and cost effective, film packaging must meet strict hygienic requirements when it is used to conserve foods, beverages and pharmaceuticals. Thermoformers from packaging machinery specialist VARIOVAC meet these requirements considerably faster than other comparable machines on the market thanks to a technology package from B&R.

Quite often, it's the little things that determine the success of a product. In the case of film packaging, one of these decisive details is the haptic experience of opening them. "How many times have you struggled to get a grip on the pull tab or had it rip off and leave you stabbing at the package with a knife?" asks VARIOVAC production manager Thomas Charwat.
To prevent these unpleasant consumer experiences, the process parameters must be maintained precisely, even at high speeds. There's a lot of know-how involved at every step along the way, such as creating the lower tray out of base film. "With our patented RAPIDAIRSYSTEM, we're able to achieve premium quality while maintaining maximum productivity and minimal material consumption," says Charwat proudly. The only way to meet these requirements simultaneously is with a high-performance automation solution.
Ergonomic operator panel accentuates machine design
Founded in 1970 east of Hamburg in Zarrentin, Germany, the machine builder and its 150 employees develop each new product with a focus on appealing design and user-friendliness. The transition to a new B&R automation system in 2010 was no exception, resulting in a customized VARIOVAC operator panel. "That was actually where the whole project started. We wanted to give our products a distinctive design and saw that B&R would allow us to do that," says Dirk Schumacher, VARIOVAC's chief electrical engineer. "It was only then that we began to realize that a B&R automation solution would allow us to do a whole lot more."
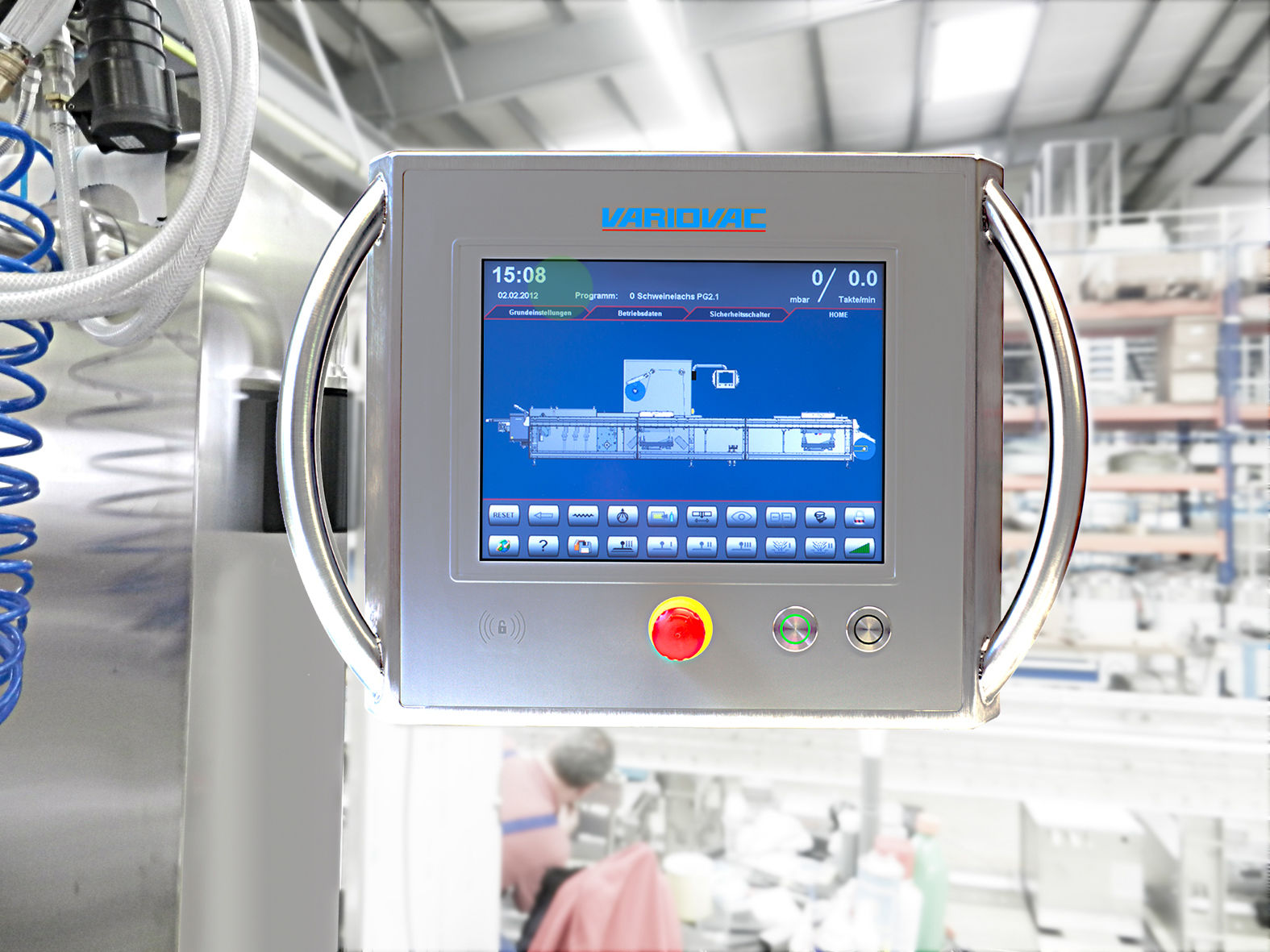
The advantages of integrated control
Replacing its heterogeneous control system with an integrated one brought the developers numerous advantages. Schumacher points in particular to the newly gained ability to execute a variety functions directly on the servo drive – such as precisely positioning the cover film for registration mark control. "Moving more intelligence to the drives lets us work faster while at the same time improving quality. We're also able to do all of our development with a single tool and have remote access options that allow us to offer our customers exceptional service."
Though designed to specific customer requirements, machines in this relatively conservative market segment have very few options to stand out through unique selling points and must instead rely on performance, quality and high-availability to compete. That's why the company is now using B&R technology in every machine series it builds. This includes not only its flagship thermoformers, but tray sealers and leak testers as well, which can be combined with other equipment such as labelers.
B&R software package stands for quality
The range of potential packaging materials – some of them in questionable quality – can really put VARIOVAC's engineers to the test. "In order for our customers to use what in some cases is very inexpensive packaging material, we needed a controller able to regulate the temperature to within ±1 Kelvin. We need to do that to guarantee sufficient quality when forming the tray or applying the cover film at high speeds," says Schumacher, describing the main goals in the development of VARIOVAC's high-performance Primus series.
The developers found a full set of temperature control software components in a B&R Technology Package that provides highly effective, highly robust closed-loop control and meets demands for disturbance compensation at the operating point and setpoint tracking performance. The required parameter sets are identified using a completely automated tuning process that is tailored to the requirements. "Our priorities were to create a highly precise and reliable tuning process that is quick and easy to implement," emphasizes Martin Staudecker, technical manager of B&R's automation software business unit.
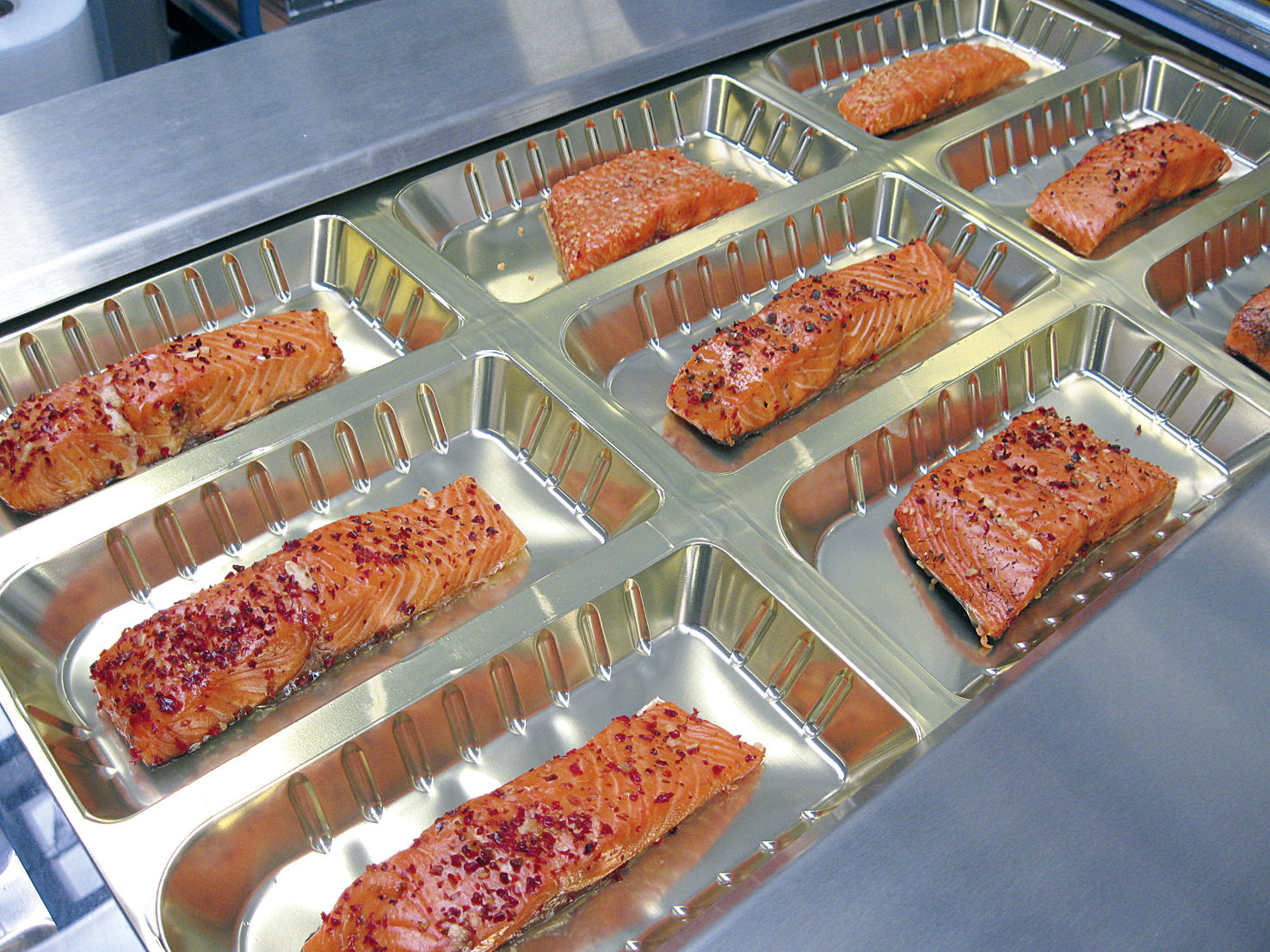
Total package seals the deal
Integrated machine control with safety technology, remote motion control, a custom stainless steel operator panel, the Automation Studio development software and comprehensive support from B&R engineers: it was the total package that convinced the VARIOVAC team. Looking at the development challenges ahead, Charwat expects a continued increase in the number and variety of axes in each machine, as well as in the demands on productivity and quality. With regard to the company's plans to continue expanding its presence globally, he concludes confidently: "With the automation system from B&R, we're well equipped for what the future holds."
Thomas Charwat Production & Quality Manager, VARIOVAC PS Systempack GmbH "The ability to rely on a single development tool and the comprehensive, straightforward support from B&R's engineers helped us reduce our development time." |