Having set its focus on bringing existing plants up to speed for Industry 4.0, the next step for Nestlé is to optimize the cost and effort involved in getting there. At its plant in Osthofen, Germany, the company has implemented a pilot project with a B&R solution that satisfies all the requirements it has outlined for the transition: the Orange Box. This elegantly simple solution helps brownfield sites take a giant leap towards smart-factory effectiveness.

Nestlé averages one or two new greenfield plants each year, such as the one in Schwerin, Germany, that began operation in 2014 and now produces hundreds of millions of coffee capsules per year. The Schwerin plant relies on the absolute latest technology to ensure that the coffee produced there is up to the highest quality standards. "While today's greenfield developments are indeed equipped with highly advanced technology," notes Nestlé MES / E&A Engineering Manager Ralf Hagen, "what you have to keep in mind is that they don't yet have the level of standardization envisioned by Industry 4.0. There's still a lot of work to be done in that area."
Seamless connectivity in smart factories
After all, in addition to the one or two highly productive greenfield plants built each year, there are also the 430 brownfield plants to deal with. "We need to be able to achieve competitive levels of productivity at those sites as well," says Hagen. "And that means optimizing them for the demands of Industry 4.0." Some of the machines at these sites began operation as many as 50 years ago. "Back then, the network infrastructure was completely different from what we think about today in terms of smart factories," Hagan explains. "In a new plant, you have seamless communication that shares data with the ERP system in real time."
Describing the current situation at the existing plants, Hagen explains: "In many cases, we're still pulling data off machines manually. There are all kinds of communication interfaces, and not all of them are designed to handle our current requirements. Sometimes the data we would need to do things like condition monitoring is already there – we're just not using it."
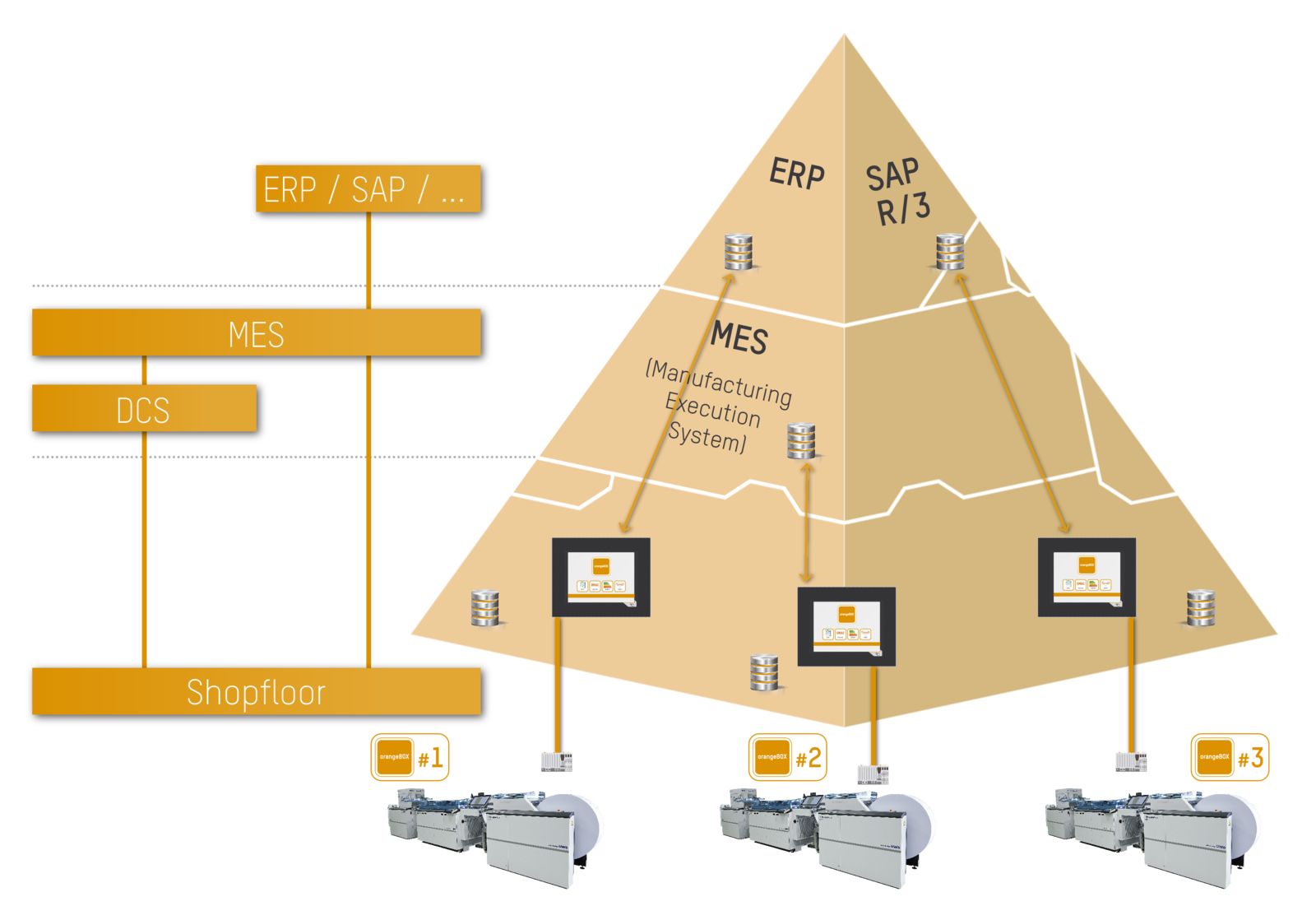
The challenge
Nestlé approached a number of automation providers with the challenge, among them B&R. Karl-Heinz Mayer, who heads B&R's technical office in Bad Homburg, Germany, identified multiple opportunities for using intelligent automation to boost the potential for optimizing existing assets. According to Mayer, when it comes to reducing the cost of production, the best metric to use is overall equipment effectiveness (OEE). "Improving your OEE score can cut production costs by 10 to 20%," he says.
Nestlé was convinced. "To get our OEE scores up, we need to significantly reduce the frequency of unplanned outages," says Hagen. "We need to have real-time access to digital production data from all of our lines. That includes not just our newer, fully integrated systems, but our older, less automated lines as well. It's also important that we have either a direct or indirect connection to the ERP system. Furthermore, the solution must be up to Nestlé's safety standards."
What they were looking for was something similar to Apple's approach: see it – tap it – it works. On top of that, it should serve as an effective intermediate solution to bridge the next three to five years until an optimal cloud solution could be found. Other challenges arise from the fact that the individual plants use different generations of control systems from different manufacturers. They also vary in the level of automation know-how available on site.
The requirements are in part based on a future with fewer and fewer skilled technical personnel. What they were looking for was something similar to Apple's approach: see it – tap it – it works. On top of that, it should serve as an effective intermediate solution to bridge the next three to five years until an optimal cloud solution could be found. Other challenges arise from the fact that the individual plants use different generations of control systems from different manufacturers. They also vary in the level of automation know-how available on site.
The solution
In light of the requirements, B&R developed a solution comprising hardware based on Scalability+ and software based on mapp Technology: the Orange Box. "The Orange Box represents an optimal combination of our modular hardware and software tailored exactly to our customer's requirements," says Mayer. "Control, HMI and mapp Technology come together to create a perfect platform for Industry 4.0 production." Customers are able to choose one of two options for connecting their machinery and equipment. They can either tap into the signals of I/O modules on third-party controller or receive data directly via ISO on TCP or TCP/IP.
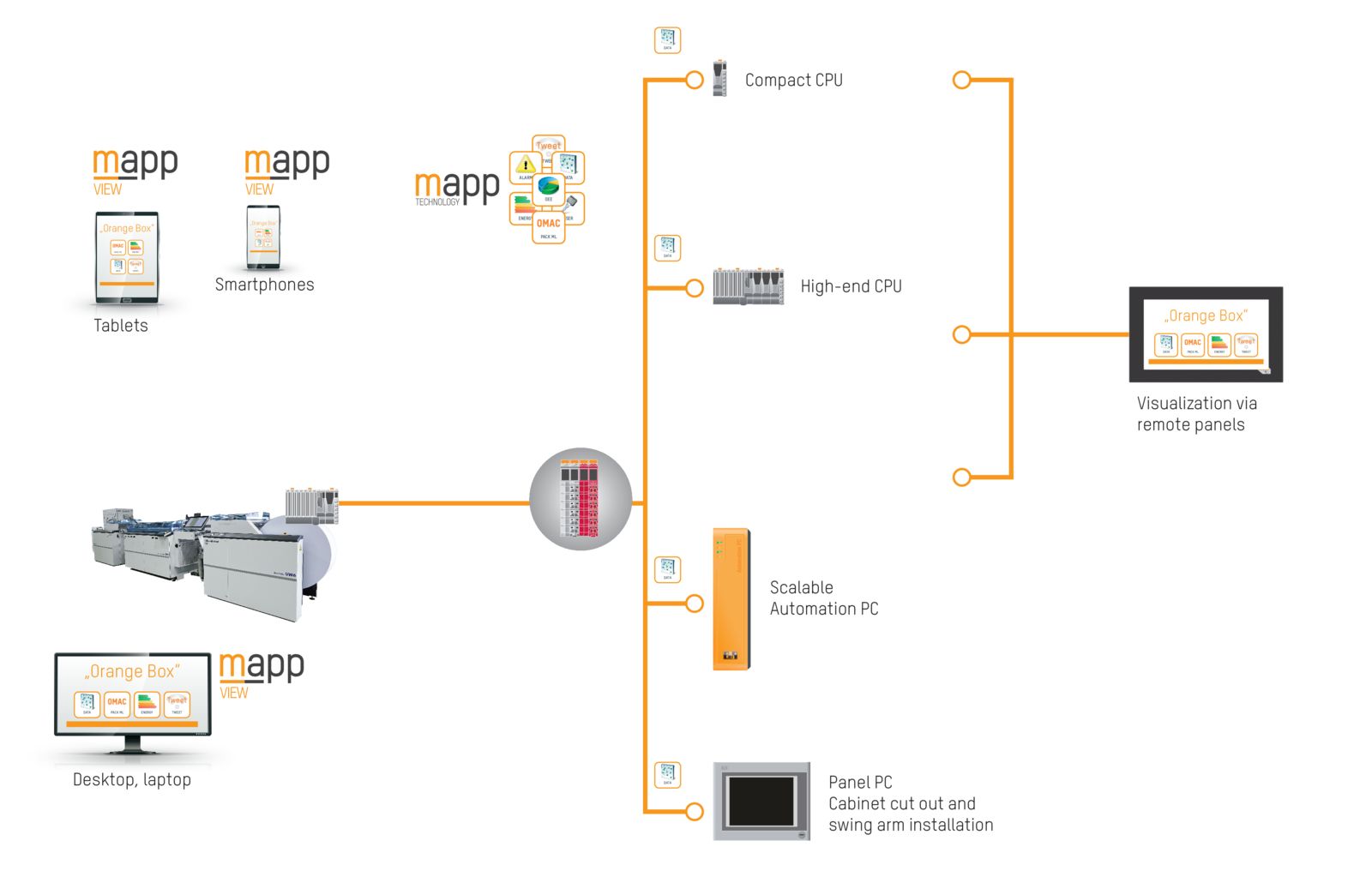
With mapp Technology, the specialists at B&R were closely aligned with the customer's requirements. "mapp Technology provides an array of standard functionality right out of the box," explains Mayer. "OEE calculation, user management, PackML, data acquisition – all these functions are available as ready-made mapp components that can be installed as easily as a smartphone app." There are some key differences between the mapp concept and the conventional function block approach. "mapp components are interactive – they can be linked together and exchange data automatically," says Mayer. As an example he describes how the mapp Energy component evaluates energy consumption data it obtains from other mapp components.
What is Scalability+?
B&R solutions are built from a fine-grained selection of homogeneous products that cover every area of automation. And whether you're talking about a standalone machine, an integrated production line or an entire factory, they are implemented using the same universal software tool: Automation Studio. By seamlessly combining integrated automation, software packages and machine technology, B&R opens up a whole new generation of machine automation.
mapp components are seamlessly integrated into the B&R Automation Studio development environment. They are easy to configure and relieve the developer of having to program every single detail. Another important facet of mapp Technology is the mapp View HMI solution. "Automation engineers have all the tools they need to create powerful and intuitive HMI solutions. There is no need for them to deal directly with HTML5, CSS or JavaScript technology," says Mayer. Based solely on web standards, B&R's HMI solution ensures optimal viewing on any device.
It is also easy to link controllers from other vendors to the HMI application via OPC UA. "With menu-guided operation and configuration instead of programming, we were able to satisfy one of Nestlé's main requirements: installation by non-specialists," notes Mayer. "We've also given them the ability to manage their software centrally – performing installation, backups and updates either over the network or via USB." Communication can take place over various channels, such as LAN or WLAN. In terms of protocols, the solution relies on standards like OPC UA and ISO on TCP.
Pilot plant Osthofen
The first pilot application for the Orange Box is underway at the Nestlé plant in Osthofen, Germany. The plant's 300 employees produce sip-feed oral supplements sold by Nestlé Health Science to help patients with special nutritional needs. "The complete scalability of both its hardware and software make the Orange Box compatible with every machine and line we have here," says Hagen. "And in terms of connectivity, the commitment to open standards provides the solution with flexible connections to process control systems – whether it's B&R's APROL or a third-party solution – as well as an MES like the plant's Wonderware system." In addition, installing the Orange Box doesn't require any modifications to legacy software.
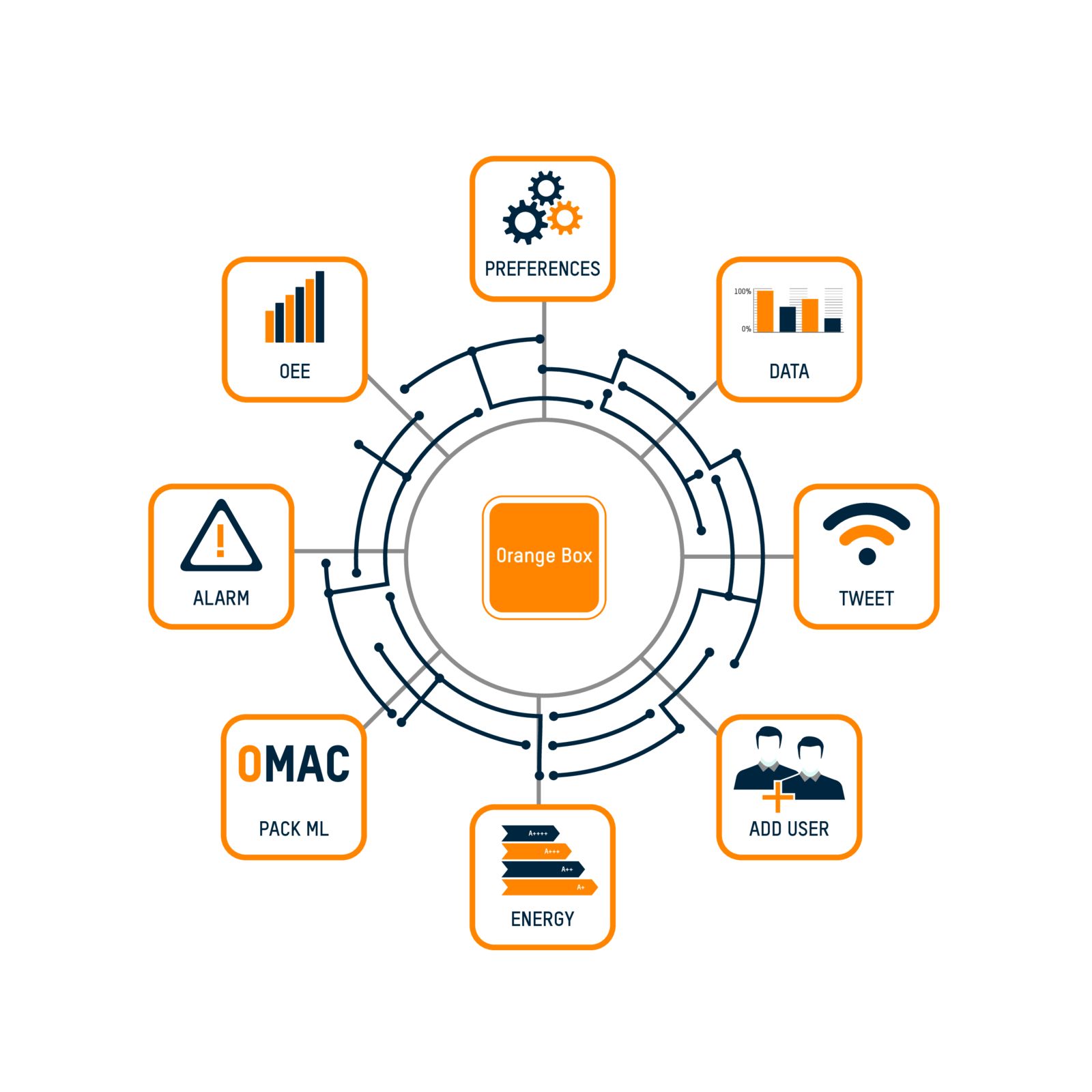
"The system is so straightforward there's no need to call in an expert. The menu guides you intuitively through every operation," emphasizes Hagen. Raw data from the machine can be collected locally in digital form. Security can be implemented either as a standalone solution or via the protocols provided by standard IT systems. "With a relatively small investment, the Orange Box gives us immediate transparency and lets us make targeted improvements that are well informed and highly effective. It's also exceptionally modular, so we can easily adapt or expand it at any time. It's everything we were looking for," concludes Hagen.
Author: Inge Hübner, VDE VERLAG GMBH, www.digital-factory-journal.de
![]() | Ralf Hagen E&A Engineering Manager, Nestlé Germany "The Orange Box gave us immediate transparency into our production data. The system is modular and can be adapted at any time. It's everything we were looking for." |