
The Great Pyramid of Giza, built in honor of the pharaoh Cheops, is the oldest of the world's seven ancient wonders. In Bern, Switzerland, however, the name Cheops is now associated with a much more modern marvel. The CHEOPS project – short for CHaracterising ExOPlanet Satellite – is being led by the Center for Space and Habitability at the University of Bern in partnership with the European Space Agency. In a few years, this satellite-born photometric observatory will provide valuable assistance in the search for planets capable of supporting life. The system's spaceworthiness is assessed through automated testing performed using advanced B&R technology.
The solar eclipse viewed in Switzerland in March of 2015 is still fresh in people's minds. A solar eclipse occurs whenever the moon passes between Earth and the sun. During a total eclipse, the moon covers approximately 70% of the sun's surface. The same thing happens when any planet passes in front of its star as viewed from Earth. In this case, however, far less than 1% of the star's surface is covered, causing only a tiny dip in the intensity of its light. The CHEOPS telescope is designed to measure this deviation and use it to calculate the diameter of the passing planet.
Before any new satellite is launched, it must be thoroughly tested under space-like conditions. In close cooperation with B&R, the Center for Space and Habitability (CSH) in Bern has constructed a fully automated thermal vacuum testing chamber for this purpose.
The CHEOPS project
At CSH, a team of 20 employees is hard at work developing, constructing and testing CHEOPS under the guidance of Prof. Willy Benz and lead project manager Dr. Christopher Broeg. The CHEOPS project is the first satellite project where the responsibility lies solely in Swiss hands. A number of different universities and space agencies are involved in various capacities. The German Society for Aeronautics and Astronautics (DGLR) and the Space Research Institute (IWF) in Graz, Austria, are responsible for the electrical subsystems, for example.
The telescope's objective is to investigate known planets that circle distant stars far beyond our own solar system. Known as exoplanets, they are identified in advance by ground-based observations using a technique called Doppler spectroscopy. The additional size data generated by CHEOPS will allow researchers to deduce the planets' density and likely composition of gas, rock and ice. The hope is that this will identify which planets are most likely to support life. With future telescopes, it may one day be possible to search the top candidates more closely for specific signs of life. The CHEOPS satellite is slated to launch in 2017.
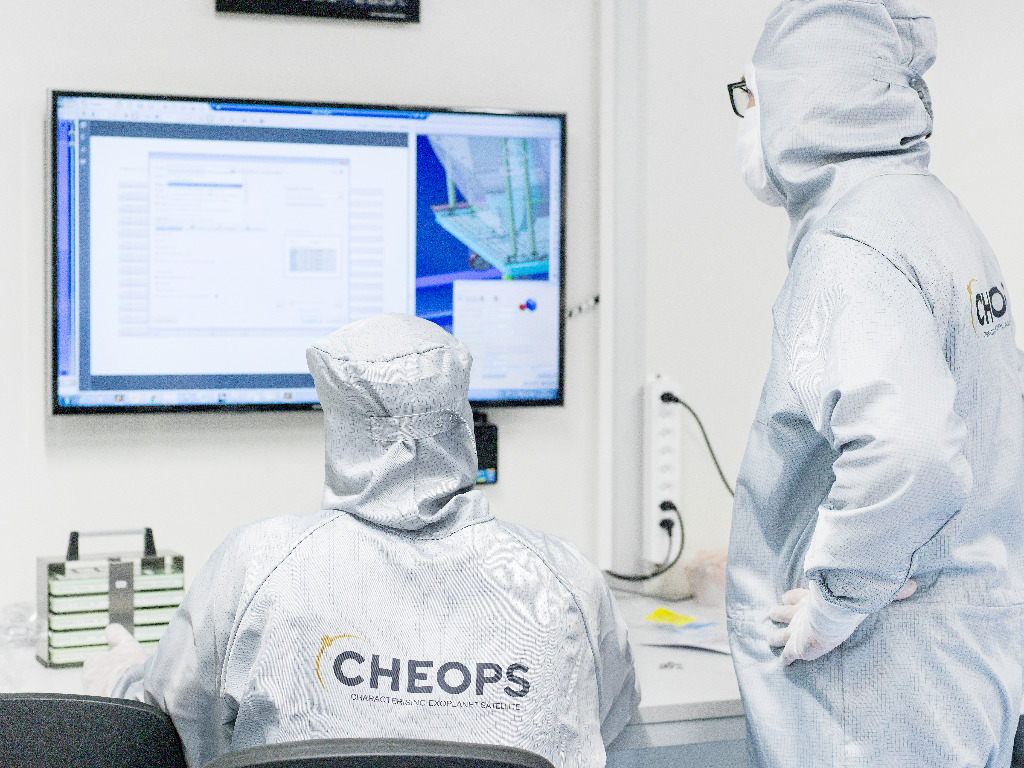
The thermal vacuum chamber
Before the satellite is sent into orbit, it needs to prove that it is fit for the task. After all, it will be subjected to some fairly extreme conditions. The telescope and and the satellite that carries it will have to withstand a vacuum of 10-7 millibars and temperatures ranging from -80°C to +165°C. To simulate these conditions, the University of Bern developed a thermal vacuum chamber. Measuring 2 by 4 meters, the chamber can hold the entire satellite platform and telescope.
The various components of the vacuum chamber – roughing pumps, turbo pumps, thermal shrouds, Huber thermostats, a solar simulator and liquid nitrogen radiators – must frequently be reconfigured with new settings throughout the course of testing. It is also incredibly important to protect the equipment being tested. Alone the structural model of the satellite currently being tested is worth more than half a million dollars.
The requirements
The thermal vacuum chamber is situated in a clean room to protect the sensitive optical elements. Since it is impossible to enter the clean room without contaminating the highly purified air, the testing chamber needs to be automated as much as possible to minimize the need for human interference.
When it came to selecting automation components, the focus was on reliability, safety, cleanliness and flexibility. It would also be necessary to connect to a higher-level Supervisory Control and Data Acquisition (SCADA) system as well as leave open interfaces for future expansion. In the interest of establishing a successful partnership it was also important that the supplier provide excellent support and have an interest in the scientific subject matter. After evaluation of various suppliers, the choice fell in favor of B&R.
The test lab
When the thermal vacuum chamber is switched on, its first task is to generate a vacuum. It does this by opening all the corresponding valves and activating the roughing pump, which creates an initial vacuum of 10-2 millibars. Subsequently, 2 turbo pumps further refine the vacuum. Once a sufficient vacuum has been established, the necessary temperatures are generated using the thermal shrouds and solar simulator.
Around 150 temperature sensors provide information about the temperature distribution inside the chamber and on the surface of the test object. If the object grows too hot, the temperature must be reduced to prevent damage to the satellite and its electronic components. Now the chamber is ready to examine the strain on the test object caused by the extreme temperature variations. Since they are made of glass, the mirrors of the telescope don't expand in the same way as the mechanical supports. This could result in serious damage. It is therefore very important to measure how the area around the mirrors is affected by space conditions in order to determine how to compensate appropriately.
The temperature is also monitored on the outer casing of the thermal vacuum chamber. The casing is equipped with a heating system that can be activated to prevent condensation.
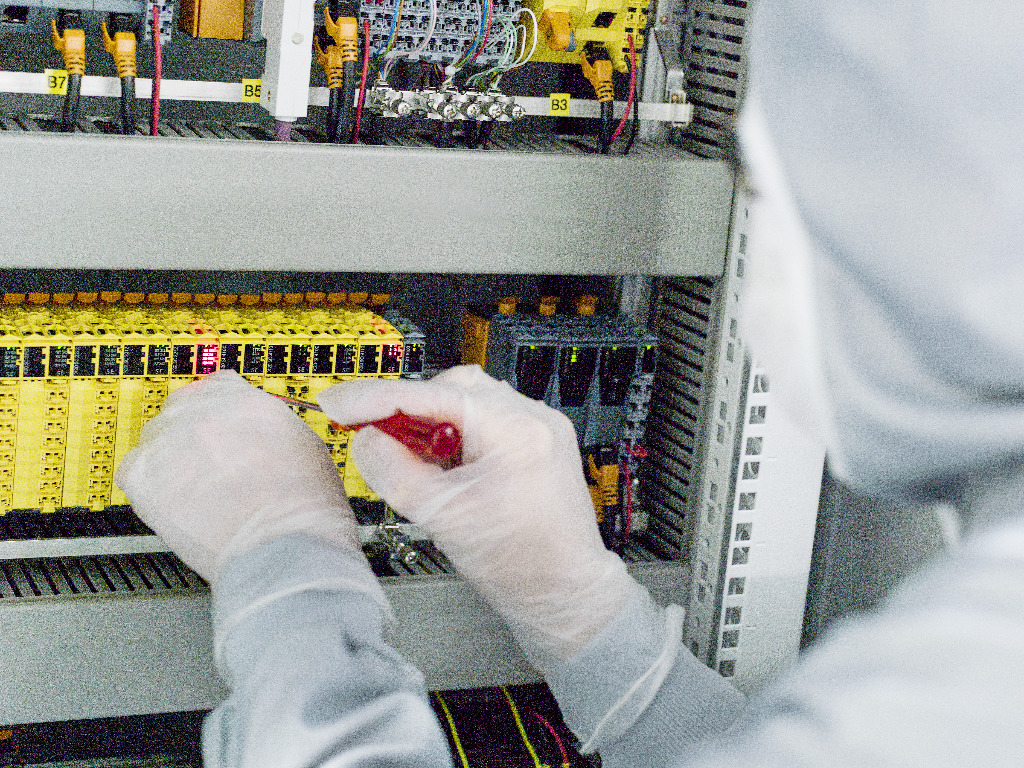
The architecture of the B&R automation solution
B&R's automation solution is comprised of the X20 system with an X20CP3586 CPU as well as an X20SL8100 SafeLOGIC controller with cable redundancy, a combination of standard and safety I/O modules for temperature and valve monitoring and an interface for the turbo pumps. Using the OPC UA protocol makes it possible to connect with the higher-level SCADA system.
Dividing the solution into 6 subsystems allowed a portion of the automation components to be placed in a machine room next door to the clean room and reduced the number of cables required. Considerably reducing the number of components in the clean room also contributes to the level of air purity. In addition to the controller, the control cabinet inside the clean room also houses serial and Ethernet interfaces, as well as the unit for evaluating pressure measurements received via a serial interface. The controller itself operates fanless and doesn't generate any dust. The components have also proven to be so clean, that it wasn't even necessary to include a filter in the control cabinet. The system is operated using a B&R terminal in the clean room. This is where the temperatures are set and the results are evaluated.
Recently, B&R's Unit Test solution was added to check the automation system at the beginning of each series. Programming is done in C or C++, the predominantly used languages at the institute.
To determine whether the satellites are prepared for deployment in space, they are tested in a manual thermal vacuum chamber. This chamber is operated using a controller and other modules from B&R's X20 system.
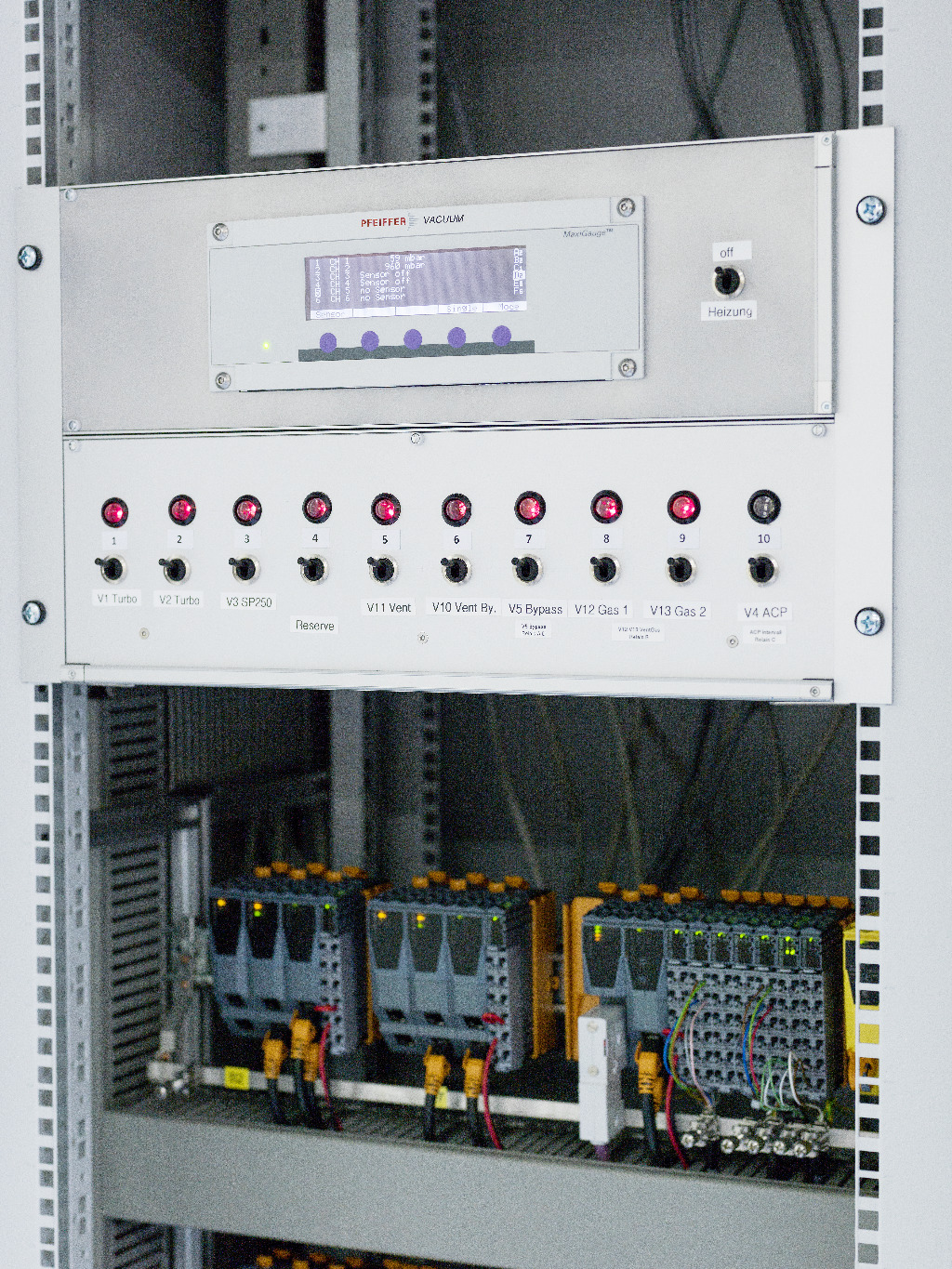
Future lab equipment
"The modularity, flexibility and real-time capability offered by B&R's automation solutions are why they are valued so highly in the academic arena," says Severin Oeschger, who is responsible for automation systems in the thermal vacuum chamber at the University of Bern. "B&R's reliable service, active R&D cooperation and keen interest in science and research were also decisive factors in our decision to team up with them on this and other projects." With the goal of standardizing architectures and consolidating suppliers to minimize overhead, the Center for Space and Habitability and the Space Research & Planetary Sciences Division at the University of Bern will be equipping new lab equipment and future expansions with B&R components whenever possible.