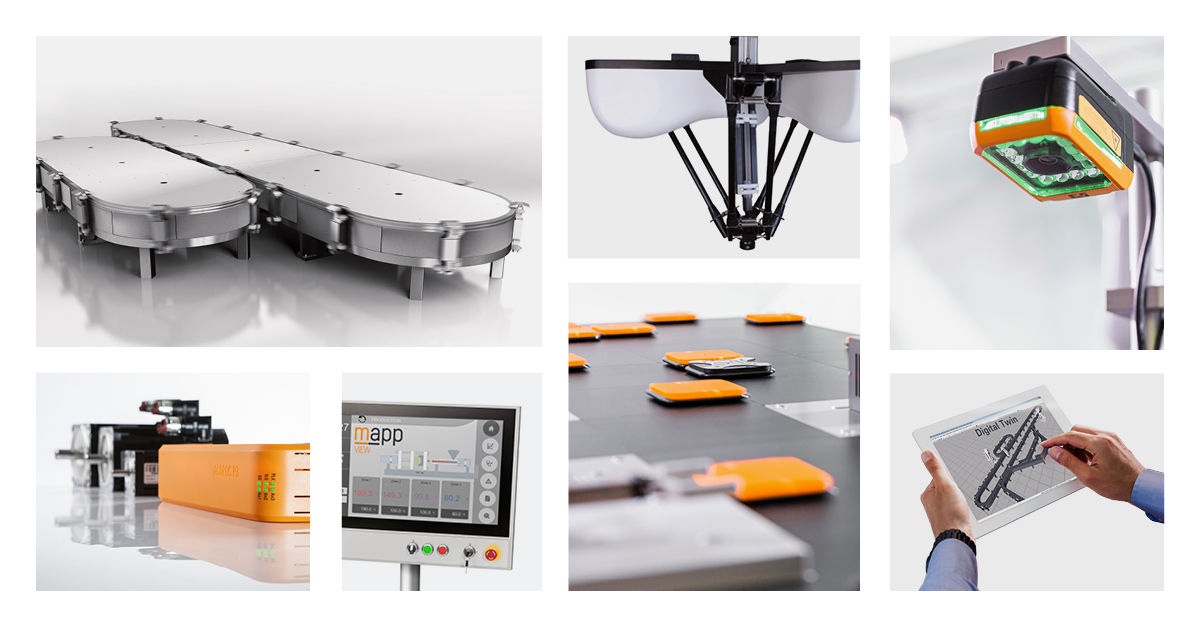
The right combination of today's most advanced automation technology - fully interconnected and integrated - gives manufacturing systems unprecedented powers of adaptability.
Mechatronic product transport – The adaptive backbone
Track-based and planar product transport systems enable continuous control of each product’s movement through a dynamic manufacturing process. Multiple shuttles synchronize with variable spacing to carry products of any shape. Electromagnetic diverters split and merge production flow at full speed. Modular segments allow unlimited layout possibilities and easy scaling and reconfiguration.
Robotics and machine vision – Hand-eye coordination
With perfect synchronization of lighting and image capture, machine vision detects the shape and orientation of passing products. Robots can adapt their movement and shuttles can adjust their spacing to perform highly precise processing and handling operations while in motion at high speeds.
Simulation and digital twins – Where it all begins
Adaptive manufacturing starts with simulation-based design. See the system in action, test feasibility and visualize its potential, all without any investment in hardware. The same simulation later serves as proof of concept for performance benchmarking. Over the lifetime of the machine, a digital twin makes it possible to refine and verify processes offline before implementing them on the shop floor.