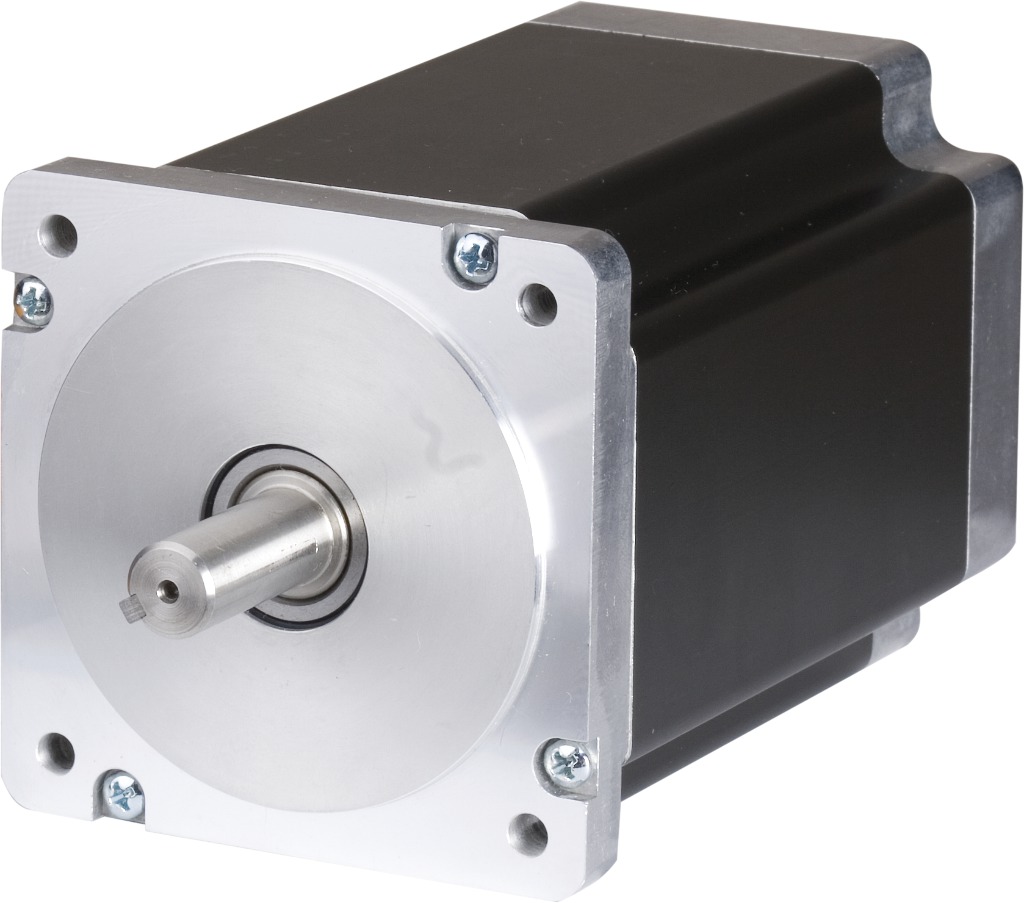
The market demands cost-effective solutions. To meet this demand, B&R offers their stepper motors as an inexpensive and powerful addition to their existing product portfolio.
- High torque
- High overload capability
- Cost-effective encoder option
- Operation in parallel and in series
- Optional IP65 protection
- Optional holding brake
Stepper motors without encoder
Stepper motors without encoder IP65
Stepper motors with incremental encoder IP20
Stepper motors with incremental encoder IP65
Stepper motors with incremental encoder and brake IP65
Stepper motors with SSI encoder IP65
Stepper motors with SSI encoder and brake IP65
Stepper motors with Hiperface encoder IP65
Incremental encoder cables
Inc. encodercables M12
SSI encoder cables
Hiperface encoder cables
Motor cables
Motor cables M12
Motor cables with brake
Hiperface motor cables
Hybrid cables
Accessories

Documentation
80MP stepper motors
Stepper motors 80MP are available in different sizes (D, F and H). These differ in dimensions (especially flange dimensions) and power data.

Additional information
80MP stepper motors
80MP - Order key
Downloads
80MP user's manual
EU Declaration 80MP
UK Declaration 80MP
UL Certificate of Compliance 80MP
Online tools
CAD configurator For motors and gearboxes. Our CAD application allows you to access 2D/3D CAD data in many different formats.
Motor data
80MPD | 80MPF | 80MPH | |
---|---|---|---|
Flange size | 56.4 mm (NEMA 23) | 60 mm | 87.1 mm (NEMA 34) |
Holding torque | 1.1 to 3.0 Nm | 1.15 to 3.5 Nm | 4.0 to 13.6 Nm |
Stall torque | 0.8 to 2.2 Nm | 0.81 to 2.5 Nm | 2.9 to 9.3 Nm |
Shaft type | Flat-sided shaft (D-cut) | Keyed shaft (ANSI 4.1) |
Areas of use
Areas of use
More than 500 million stepper motors are installed each year around the world. Although most of these motors are used in very simple applications, they are also seeing increased usage in applications that have traditionally been handled by DC and BLDC motors. High-performance controllers increasingly make it possible for more complex tasks to be solved. Many applications that were once handled using smaller servo motors can now be handled by a stepper motor outfitted with the corresponding electronics. Not only have the possibilities involving controllers advanced over the last few years, but the motors themselves are running considerably smoother and with higher torque thanks to improved technology. New, robust position feedback possibilities are becoming much less expensive and are also playing their part in opening up new areas of use for stepper motors. Of course, stepper motor solutions also have their limitations. Particularly when it comes to high speeds, which are no problem for servos, stepper motors often do not stand a chance. However, when it comes to gearbox solutions, opportunities often open up to use a smaller gear ratio or even manage without a gearbox at all. The reason for this is the high torque that can be achieved with stepper motors in the low to intermediate speed range.
Choosing the right motor
Choosing the right motor
The user faces many difficulties when it comes to choosing a motor. There are considerable differences between motors from different manufacturers or even between motor generations from the same manufacturer. The standard specifications listed in the data sheets often do not provide enough information to make a decision in this regard. Only detailed information can reliably indicate the possible areas of use. Parameters such as runout, back EMF, efficiency, resonant frequencies, etc. become more important as the complexity of the application increases. When chosen with care, stepper motors can be used for many more applications than is normally the case today. Special attention must be given to the characteristics that are particularly important for the respective application. These characteristics often cannot be achieved unless a drive is also used.
Concentricity and angular precision
Concentricity and angular precision
A majority of the 2-phase hybrid stepper motors have a stepping angle of 1.8 degrees. In addition to this however, are the versions with 0.9 degrees and the even less common with 0.45 degrees. The smaller stepping angle often results in poorer torque characteristics. However, only stepper motor drivers that support micro-steps can achieve higher positioning accuracy. Moreover, a high step resolution produces excellent concentricity properties and reduces potential problems resulting from resonance effects.
Position accuracy
Position accuracy
The manner in which the desired position is ultimately reached depends on the applied load torque as well as how accurate the stepper motor is when it is manufactured. The position accuracy within one step is always dependent on the load and the resulting angular slip. However, this can never be higher than one full step because otherwise the motor gets out of sync and steps are lost. The best way to compensate for this load angle is via position feedback. This is why all B&R stepper motors are also available in affordable encoder variations, which achieve a resolution of up to 12 bits. Therefore, positioning precision is possible with an angular deviation of less than 0.1 degrees, even under considerable load torque.