Both new and existing converting and die cutting units from machine builder Spilker can now benefit from a cost-effective, fully integrated machine vision solution from B&R. Measurement data is recorded directly in real time and used not only to fulfill documentation requirements, but also to optimize processes and improve product quality. Since all image processing occurs in the sensor, there are no interfaces to program. Quickly and easily implemented in the Automation Studio development environment, this makes the vision solution exceptionally powerful.
Fast changeovers and minimal waste with integrated machine vision at Nilpeter A/S. Nilpeter has introduced a new label printing machine that reduces customer costs and help boost earnings by using integrated machine vision from B&R Industrial Automation. The machine enables small batches quickly and make sure you end up with high-quality products, not waste. The machine builder benefits from smart series production, easy installation, only one cable, factory pre-calibration and quick configuration of the smart camera.
Registration mark detection
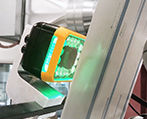
Task: Detect small, freely positioned registration marks (up to 1 mm)
Technical data:
» 13 μs exposure
» Many exposure colors, can be changed at runtime
Advantage:
» Reliable detection, even with low-contrast print colors
» Cost savings through reduction of materials and waste
Made possible by: Complete integration of the camera in the control system
Product tracking
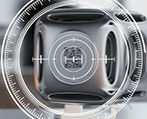
Task: Read data matrix codes on fast-moving metallic parts
Technical data:
» Product speed 56 m/s (202 km/h)
» Reflective surfaces
Advantage:
» Reliable reading at high speeds
» Integrate into automation system and put into operation in a few hours
Made possible by: Powerful lighting and tight synchronization
Labeling machine
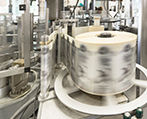
Task: Position label based on bottle seam or embossing
Technical data:
» Rotation: 450 rpm
» Throughput: 180 bottles per minute
Advantage:
» Easy configuration of optimal imaging angle
» Good contrast for fast detection
Made possible by: Switch between area and line-sensor mode on the fly
Sheet metal forming
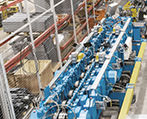
Task: Final product quality inspection
Technical data:
» Capture products up to 1.2 meters in length
» Resolution <300 μm
Advantage: High resolution and flexible changeover through integrated recipe management
Made possible by: 1280 x 4096 pixel resolution in line-scan mode
Production of personal care products
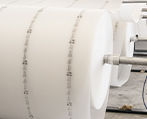
Task: Detection of print features to control register and cutting
Technical data:
» Product speed >8 m/s
» Cycle time 16.1 ms
Advantage: Fast production cycles; Fast and easy implementation
Made possible by: Microsecond synchronization and fast FPGA image preprocessing
Product tracking
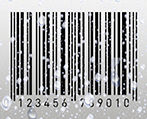
Task: Read ID (barcode or QR code) under challenging conditions
Technical data:
» Damaged/dirty product ID
» Partially wet surfaces or mist
Advantage:
» Reliable code reading (1D and 2D) without external lighting
» Integrate into automation system and put into operation in a few hours
Made possible by: Homogeneous lighting and robust algorithms
Blow molding
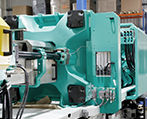
Task: Real-time control of extruder parameters
Technical data: Synchronized IR; backlight Vision fully integrated in the control loop
Advantage:
» Boosted OEE; Machine vision and HMI implemented in less than a week
» Synchronized measurement data acquisition during runtime
Made possible by: Precise synchronization between machine control and vision
F&B pick-and-place

Task: Detect products on conveyor belt
Technical data:
» Backlight with 25,000 cd/m²
» Axis-synchronized image processing <1 μs
Advantage:
» Easy data handling and integrated HMI
» Added detail through synchronous back and front lighting
Made possible by:
» Extremely powerful illumination through conveyor belt
» Optional addition of synchronized camera lighting
Paper roll production
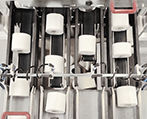
Task: Detection of defective or misaligned rolls
Technical data:
» Product speed 50 m/s
» Synchronized mechanical sorting
Advantage:
» Adaptability to product color
» changes with configurable lighting colors Prevention of downtime
Made possible by: Easy synchronization of motion control and camera system