The range an electric car can travel on each charge of its battery is possibly the most decisive factor in its acceptance among consumers. This makes rechargeable lithium ion batteries a key element of electromobility concepts all around the world. An increasing number of electric vehicle manufacturers rely on the battery testing and simulation platforms from Gustav Klein to design and optimize their battery solutions. Now, advanced B&R technology has helped the company make its systems even easier to develop, use and service.
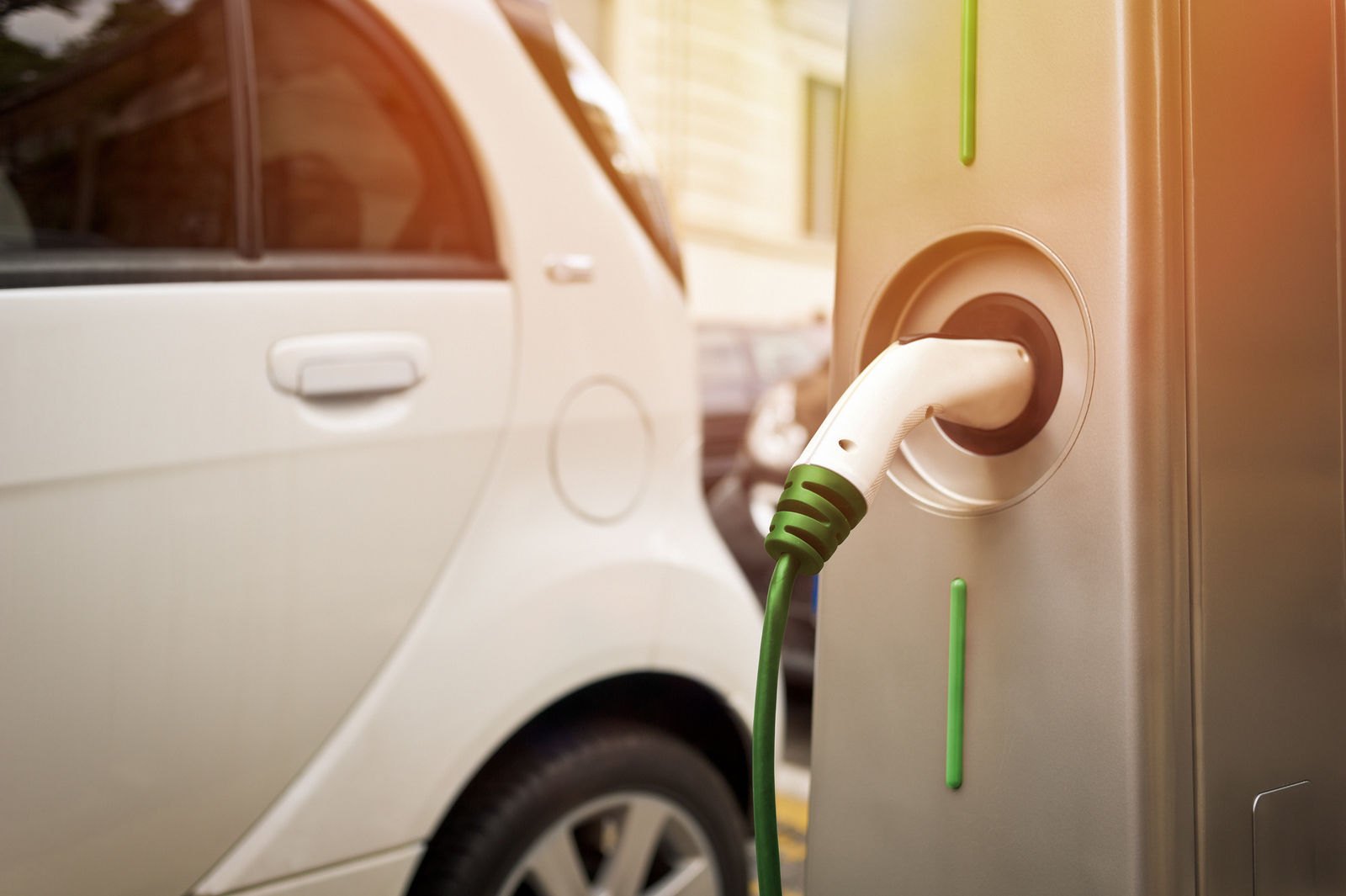
Germany has laid down the gauntlet for its automotive companies. By 2020, a million electric vehicles should be underway on the nation's streets and highways. As of January 1, 2017 the total was 34,022. Amid diesel scandals, impending inner city traffic bans and tightening restrictions on combustion engines in China and elsewhere – manufacturers are feeling the pressure from all sides to shift e-mobility into high gear.
"Things are really picking up momentum now," confirms Bernhard Rill, head of sales and marketing at Gustav Klein. Judging by the recent upsurge in interest among automotive manufacturers for the testing and simulation systems his company produces, Rill appears to be right. Automotive engineers use the Infeed Test System from Gustav Klein to assess the precise behavior of their vehicles' electrical systems and connected actuators under clearly defined and repeatable power supply conditions. "You can't do that with a real battery," explains Rill, "because of the constant fluctuations in charge level." Other uses of the Infeed Test System include the component testing performed during production of batteries and vehicles, or identifying the optimal power source for newly designed electric vehicles.
That's particularly easy with the programmable test systems from Gustav Klein. The multi-channel variants are available with an internal DC bus that allows them to be combined as needed. This makes it possible, for example, to perform a controlled discharge on one channel and use the released power to charge a battery on the second channel. This simplifies the execution of charging cycles while at the same time reducing power consumption. "To accurately simulate battery behavior, you need a very rapid slew rate," says Rill. "Our systems make the jump from -900 to +900 amps in only 1.2 milliseconds, with a seamless transition between charging and output." Current systems are able to provide an output of up to 1,000 volts or 1,000 amps (up to 500 kilowatt capacity per device).
Product variety demands strategic shift
It's been fifteen years since Gustav Klein filled the first orders for its battery simulation and testing systems. Today, the company's products make their way from Schongau in southern Bavaria to the R&D and production facilities of nearly every major automotive manufacturer in the world. The more widespread the use, however, the more varied the requirements. "We have a huge variety of system configurations being used under drastically varying conditions," says Jörg Umbreit, head of R&D at Gustav Klein. "As a result, we have to support a growing number of interfaces and manage increasing product variation."
That places some challenging demands on the control system. The control loops need to run in the microsecond range in order to achieve the necessary slew rates. At the same time, the channels must be controlled with perfect synchronization to allow parallel operation. "The need to transfer large volumes of data further complicates the matter," adds Umbreit.
In the first evaluation phase, Gustav Klein looked at five well-known controls suppliers, with B&R coming out on top. "It was the total package that convinced us," reports Umbreit. "We were particularly impressed by the performance and flexibility of the system, the universal programming environment and the quality of the support we received. At a personal level things just clicked from the very beginning."
Flexible control architecture
In 2014, Gustav Klein's engineers began developing a new control architecture for the third generation of its Infeed Test System. For the control platform, Gustav Klein selected a rail-mounted CPU module from B&R's X20 system. "We were able to use an X20 controller with relatively little memory," says Umbreit. "As the requirements increase, the scalability of the B&R solution allows us to easily upgrade to a more powerful controller without having to make any changes to the software."
The new architecture also allows Gustav Klein to more readily accommodate its customers' interface requirements. An array of X20 interface modules are available for use with the CPU module.
The control system is operated using a remote Power Panel T30 terminal display. "Since the HMI application also runs on the rail-mounted CPU module, we're able to deliver the system without a display if needed," says Rill. "That helps us keep up with the trend of users operating their systems via remote access." Either way, the user interfaces are identical and only need to be programmed once.
One software project, one engineering environment
"One of the absolute highlights of the B&R solution is certainly the engineering environment – where we were able to create the HMI application and control software all in the same project." The same applies to the integrated safety technology, which is why Gustav Klein also decided to replace its separate safety hardware with integrated X20 safety technology. That decision further simplified engineering considerably.
The switch to B&R technology brought noticeable improvements in terms of variant management and maintenance as well. Gustav Klein is now able to manage its entire testing system, including all options and future extensions, in a single software project. "Whatever is not installed, we simply disable in the software," explains Umbreit. "That way we only have one software application to test and maintain for every release."
The very positive feedback from users of the new HMI and control technology have Gustav Klein planning to carry over the HMI solution to its largest product group: its power supply systems, which include UPS modules and mains inverters.
![]() | Bernhard Rill Head of Sales and Marketing, Gustav Klein "Working with B&R is always productive, even when we approached them with complex questions or suggestions. Thanks to B&R, we now have a consistent, flexible and scalable automation system. The time and cost of integrating safety, control and HMI functionality has shrunk considerably." |