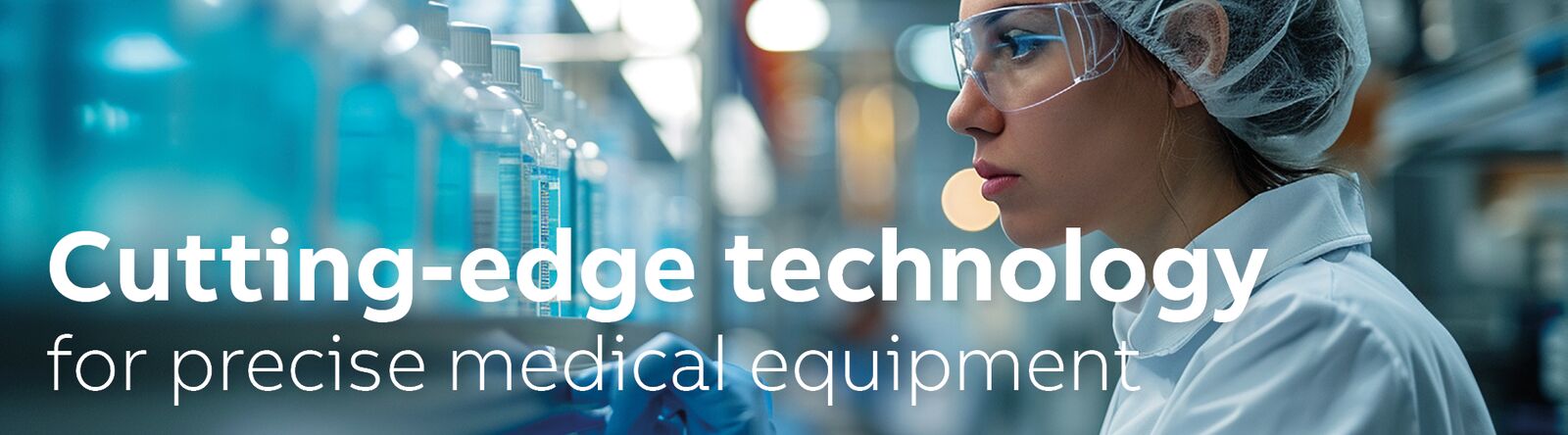
Added flexibility for the assembly of medical devices
The market for medical devices is growing rapidly, driven by an aging population in industrialized countries, improved access in developing countries and technological innovations that improve quality of life. The pandemic has accelerated this growth and highlighted the risks of semi-automated processes that rely on human labor. Unpredictable peaks in demand and the need to scale production quickly underline the importance of automation for medical device manufacturers.
From medical advances to changing markets – successful medical device manufacturers are using automation to meet the challenges of rapidly changing demand. Learn more about the challenges facing the MDA industry and how B&R is actively working to meet those challenges.
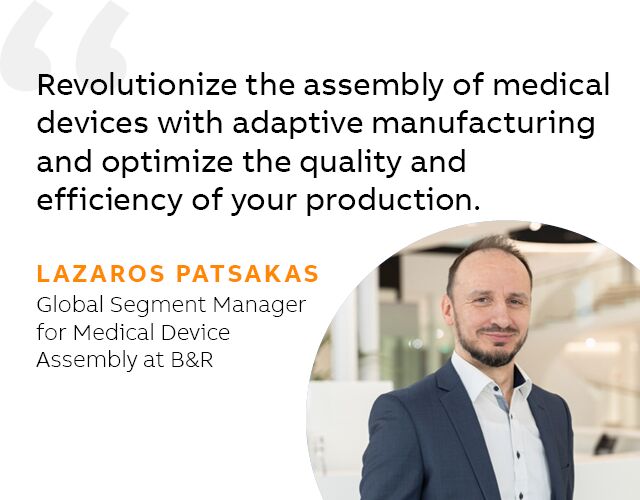


Digital technology integration
Leading manufacturers in the medical and pharmaceutical industries are working on solutions with the capability to manufacture multiple product variants. This makes it possible to produce small batch sizes without any loss of productivity. Our new generation of adaptive machines is highly efficient at automating dynamic processes. The secret: Pioneering technologies integrated into one system. With this innovative strength, B&R is the ideal partner for the medical device industry.

Personalized medicine and medical aids
Advances in genomics and molecular biology have driven the development of personalized medicine and medical aids. For personalized medicine and medical aids, state-of-the-art technologies must be integrated to ensure real-time monitoring of the entire process and 100% quality control. B&R has many years of industry experience and an innovative portfolio of products and solutions.

Control production costs
In cleanrooms, where every square meter counts, the ability to scale performance without increasing the size of the machine is a major advantage. Practical example: A B&R customer produces parts for infusion sets. Thanks to B&R's solution expertise, production could be doubled in the same amount of space. This means that customers can produce more without needing more floor space – a decisive innovation for their competitiveness and profitability.

Adaptive automation solutions for medical technology
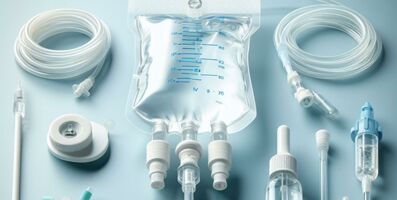
Flexibility for product changes
B&R's track systems – ACOPOStrak, SuperTrak and ACOPOS 6D – are extremely flexible and adapt effortlessly to different production requirements. Our unique shuttles and track diverters can be easily reconfigured to support different line layouts or products while maintaining real-time control of each individual product throughout the process.
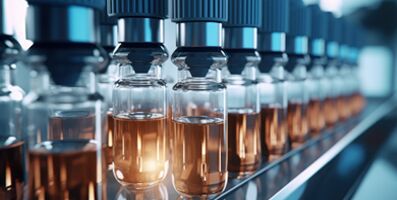
Quality control and traceability
By integrating B&R machine vision into the track systems, quality checks can be executed in real time during the assembly process. At the same time, traceability enables precise production tracking. By reducing errors and implementing real-time quality control, scrap costs can be reduced.
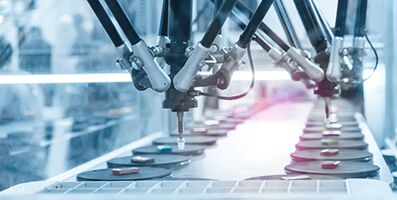
Increased productivity
B&R's expertise increases efficiency and also enables optimization and control of each individual product during the assembly process. This raises overall productivity. The result? Higher production output and the potential for significant increases in sales. Rely on B&R to take your assembly processes to the next level and strengthen your competitive edge.

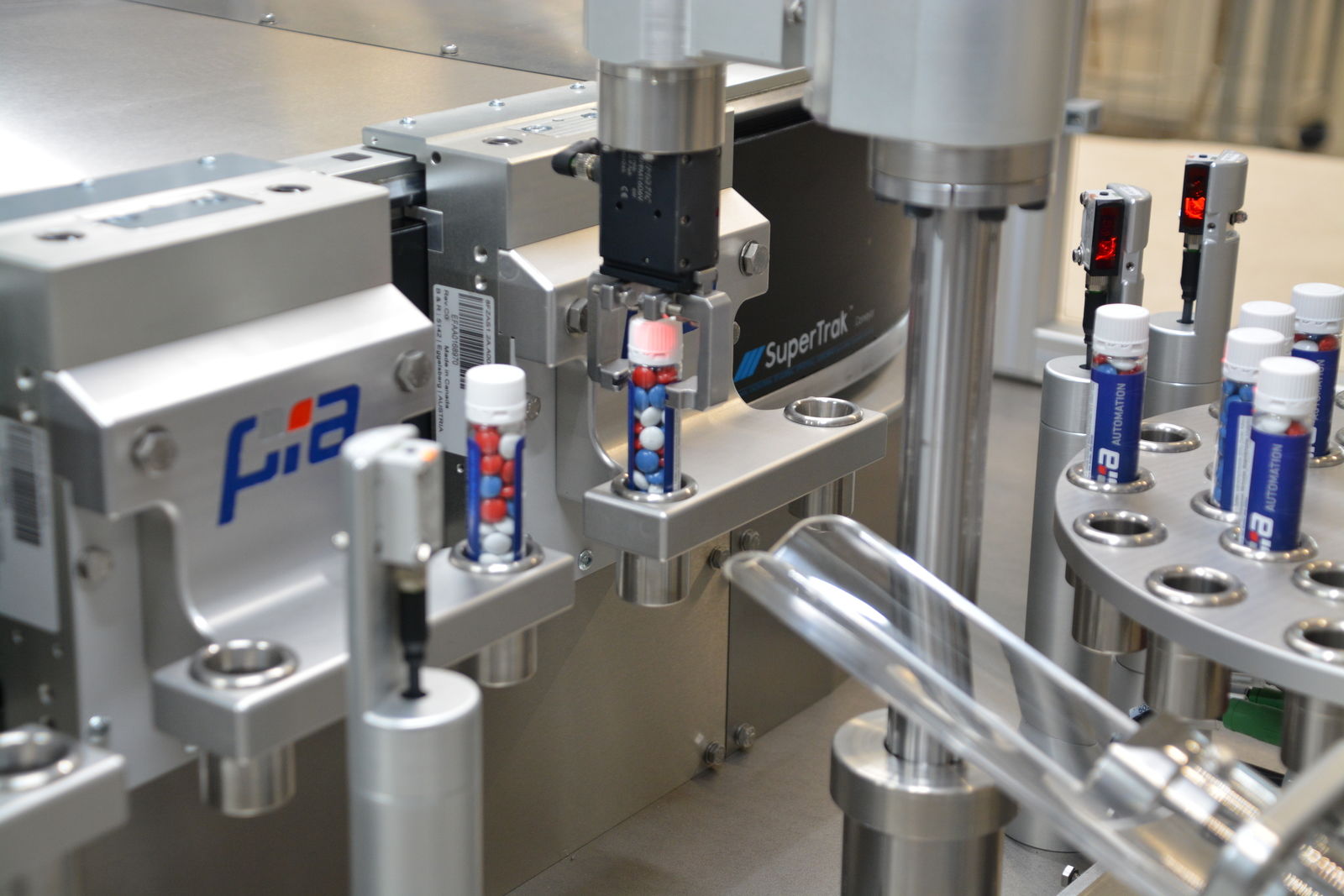
Compact cleanroom
PIA Automation uses track technology in an innovative process module for medical device assembly inside and outside the cleanroom. Find out more
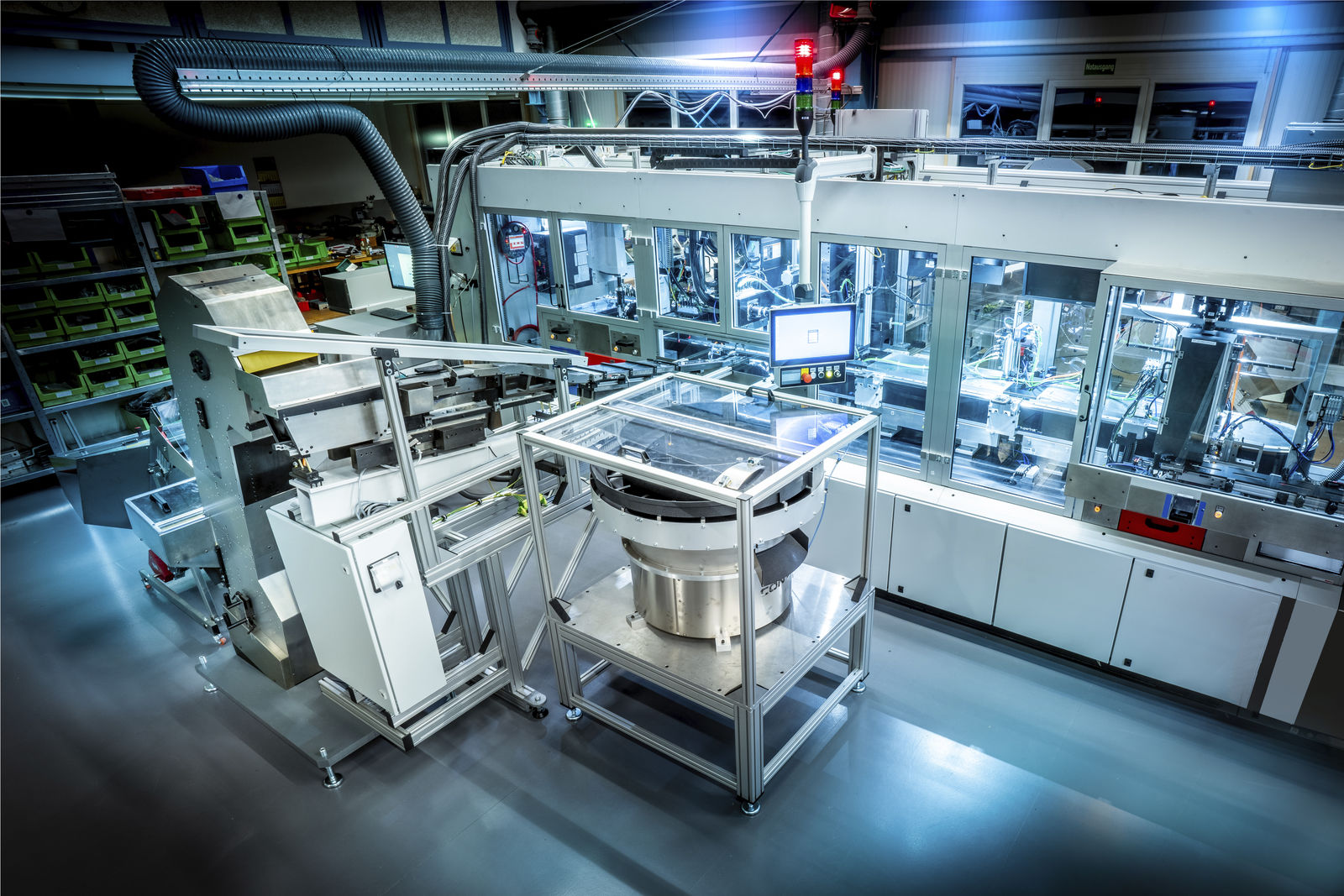
Increased flexibility
For K&S, the flexibility of independently controlled workpiece carriers is crucial to their ability to quickly react to unexpected changes in requirements or even entirely new products. Find out more
Top performance for medical devices
Tecnoideal's adaptive track system enables fully automated and fault-tolerant production of disposable products. Fast and precise positioning of the autonomous shuttles maximizes availability and productivity without compromising quality. Optimized positioning of the process stations significantly reduces the machine footprint, which results in considerable space savings in the cleanroom.
Eliminating downtime in DTO printing
Neyret Group recognized that inkjet printing can be a relevant alternative to stamping for direct-to-object (DTO) printing machines in the pharmaceutical industry. Neyret implemented the new inkjet solution with SuperTrak from B&R and now offers its customers printing machines that are fast and flexible. This minimizes downtime and increases throughput.
Future-proof productivity
By equipping its device assembly and vial capping systems with intelligent track technology IMA Automation has gained substantial flexibility and scalability, while also eliminating gaps to make optimal use of every square meter of floorspace.
Fast and precise product transport
GEAF has equipped its new machines with SuperTrak from B&R. The products can now be transported through the system quickly and precisely. As there is no wear or contamination, so the system is ideal for use in clean rooms.

The demand for small batch sizes and customized pharmaceuticals is continually increasing. At the same time, production costs should fall and overall system effectiveness increase. Adaptive solutions for medical device assembly are therefore more in demand than ever.
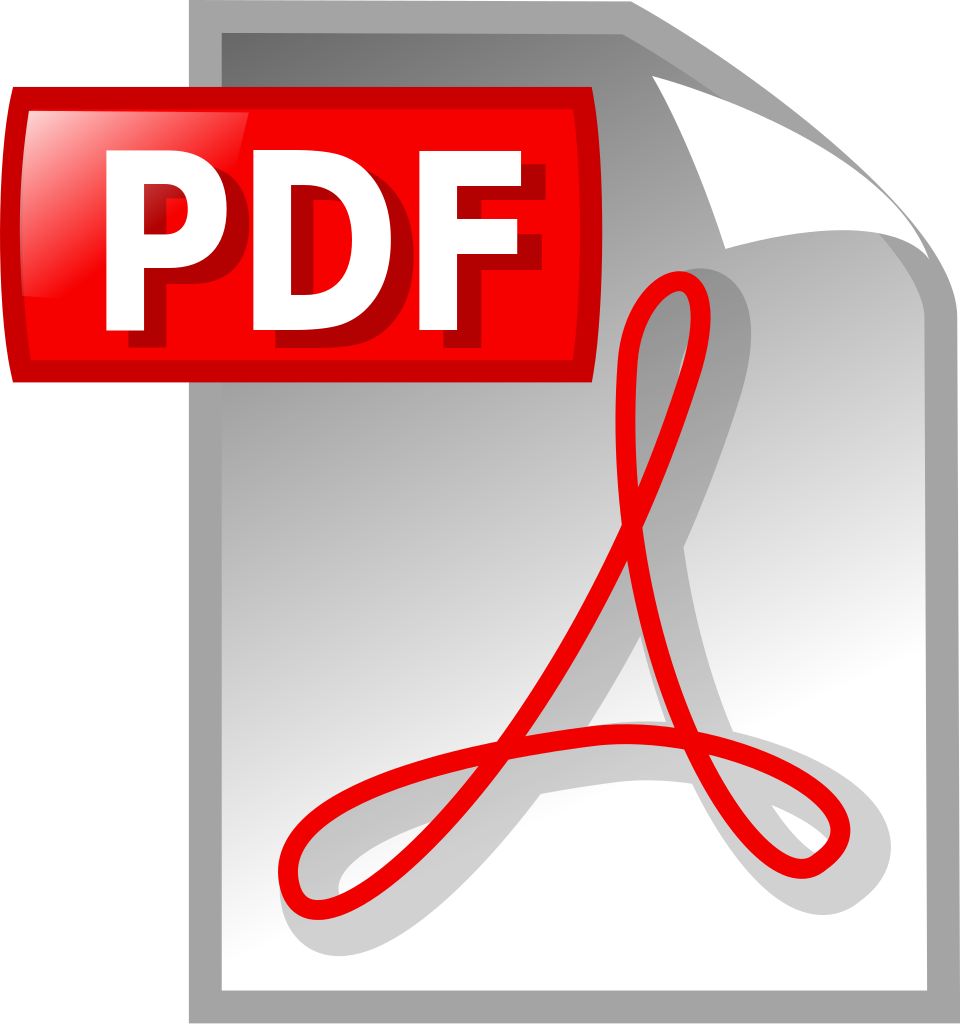
The e-paper summarizes the challenges facing the industry and opinions on adaptive machines:

Do you have any questions? – Talk to an industry expert

Additional contact options for B&R: Local value provider

Find a partner near you
Take advantage of our global network for end customers.
In addition to more than 200 B&R subsidiaries in over 70 countries around the world, we have a global network of Value Providers. B&R Value Providers work seamlessly with B&R to bring our products and services to your location. They combine in-depth knowledge of B&R technology with a deep understanding of your local market.